MecAut - Cabos de vela
- Drano Rauteon
- 16 de jan. de 2022
- 16 min de leitura
Atualizado: 13 de jan. de 2024

Imagem 1 - Motor SPE/4 da GM com bobinas individuais e cabos de vela
De maneira muito simples, um cabo de vela serve para fazer a ponte de ligação entre a vela de ignição e a bobina de ignição. Como sabemos, a câmara de combustão de um motor é preenchida com a mistura Ar / Combustível e precisa de uma centelha para que haja a combustão e consequentemente a geração de calor e movimento. Mas, para que ocorra a ionização da mistura A/C comprimida é necessário uma descarga elétrica com uma tensão demasiadamente alta, pois apesar dos eletrodos da vela estarem muito próximos um do outro, a resistência elétrica provocada pela mistura comprimida é extremamente grande. É aí que entram as bobinas de ignição.
Como a tensão fornecida pela bateria e alternador para todo o circuito elétrico do veículo não é suficiente, a bobina de ignição é necessária para "amplificar" esta força e então gerar a descarga necessária para a vela de ignição proporcionar a centelha que vai ionizar a mistura A/C e, consequentemente, a combustão no cilindro.
E a primeira publicação de 2022 é dedicada ao estudo destas pontes de ligação entre vela e bobina. Começamos com um pouco de história...
No início da indústria automobilística, a eletrônica era muito rudimentar, não existia sistemas de controle computadorizados, portanto a bobina de ignição era única e havia um sistema mecânico de distribuição de energia, que alimentava todas as velas. Este sistema é composto pelo famoso “distribuidor” e "platinado".
A ligação da bobina no distribuidor, bem como a ligação do distribuidor em cada vela de ignição é feito por cabos.
Com o passar das décadas, mais sensores foram colocados nos motores, surgindo então a “ignição eletrônica”, que elimina o sistema mecânico de distribuição, porém os cabeamentos continuam sendo utilizados.
Com a chegada da injeção eletrônica, possibilitou-se a colocação de mais bobinas alimentando as velas, como é o caso do motor Renault F3R ou da linha GM VHCE, ambos projetos contemplando um par de bobinas para quatro velas,
Até que chegamos nos dias de hoje, onde cada vela possui sua própria bobina de ignição acoplada em sua extremidade superior, tornando a conexão (cabo de vela) entre bobina e vela mais curta e melhorando assim o desempenho dos motores. Você verá mais sobre bobinas "canetão" ao ler todo este texto.
CURIOSIDADE: Há exceções, pois alguns motores com bobinas individuais para cada vela ainda fazem uso de cabos, como é o caso dos SPE/4 1.0 e 1.4 8v da GM, mostrado na foto de capa deste artigo.
No entanto, toda essa evolução de décadas "ainda é muito recente", e os cabos de vela são amplamente comercializados, pois desde carros como o Fusca (que possui distribuidor), ou então veículos equipados com o já mencionado SPE/4 (que possui injeção eletrônica com bobinas individuais) utilizam cabos de vela.
Você pode estar imaginando: “mas qual o motivo de se falar sobre um simples pedaço de fio que interliga uma bobina e uma vela?”.
O assunto não é tão simples assim. Talvez fosse lá no princípio da indústria automobilística, onde os motores Flat Head tinham uma taxa de compressão não muito alta e, portanto, as velas de ignição não requeriam uma tensão de excitação tão elevada, fazendo-se necessário apenas simples lâminas ou cabos com fio de Cobre as conectando ao distribuidor, como é o caso do propulsor da figura seguinte:

Imagem 2 - Propulsor de um Ford AA produzido em 1931. Perceba as lâminas - que sequer são encapadas - conectando as velas nos terminais da carcaça do distribuidor
Agora, observe a imagem do motor de um GAZ-51, caminhão soviético lançado em 1946. É um quatro-tempos de 3,5 litros distribuídos em 6 cilindros, nada mais que um Flat Head americano (só que licenciado e aperfeiçoado pela URSS). Os cabos de vela são encapados, assemelhando-se fisicamente com os da atualidade:
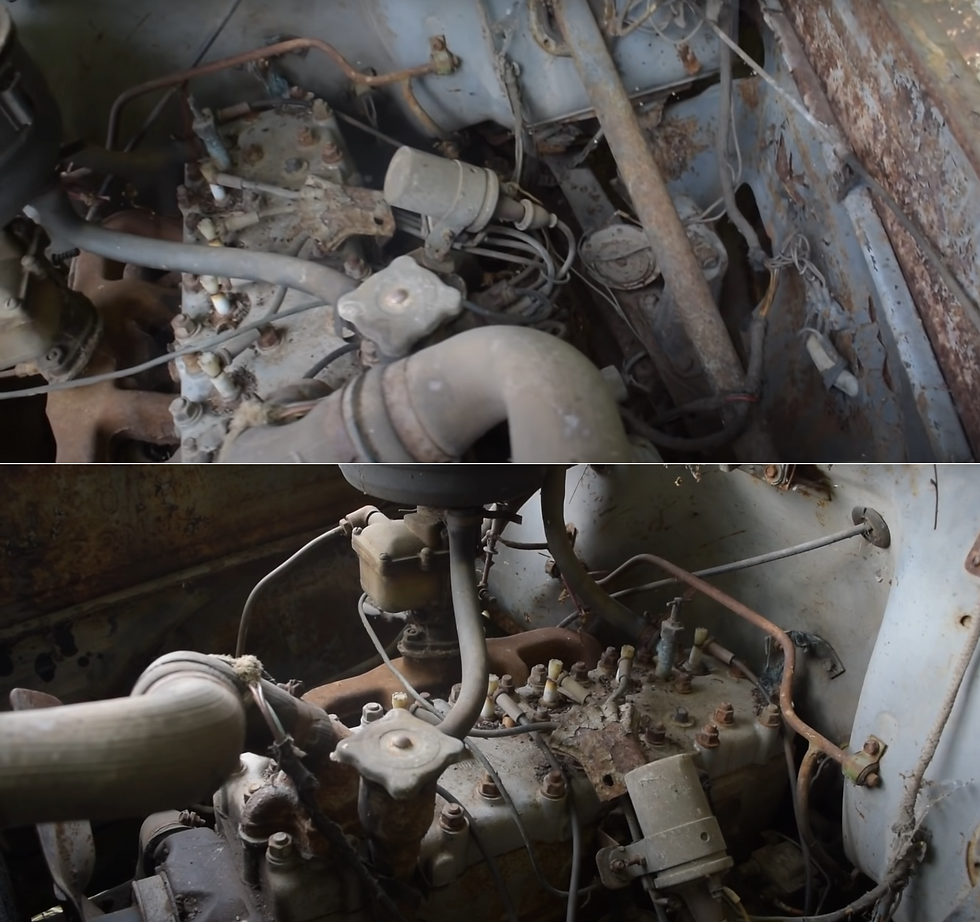
Imagem 3 - Em 1946 já era um defasado motor americano, no entanto, recém aperfeiçoado pela URSS ele foi produzido por vários anos
Todavia, os motores foram evoluindo e a energia necessária para ionizar os gases comprimidos na câmara de combustão aumentou substancialmente, e foi este um dos problemas que levou a engenharia a pensar em como reduzir a interferência eletromagnética gerada pelas fiações elétricas.
CURIOSIDADE: O assunto são cabos de velas, no entanto, por uma questão de curiosidade, nos anos 1970, com o surgimento do sistema ABS (criado pela Bosch), os primeiros veículos da Mercedes equipados com tal tecnologia sofriam alterações no desempenho das frenagens ao passar por determinados trechos da Autobahn (as autoestradas alemãs). Este é só um exemplo de que perturbações eletromagnéticas externas podem afetar sistemas eletrônicos automotivos. Agora, imagine o cofre de um veículo, com um motor de combustão interna requerendo tensões na casa dos 30 kV para a ionização da mistura A/C, e tudo isso com o mínimo de interferência nos sistemas eletrônicos operando ao redor.
O grande porém é que não existem meios físicos de se evitar que uma perturbação eletromagnética seja propagada ao restante do sistema. O que a engenharia automobilística passou a fazer foi, simplesmente, “blindar” o sistema, evitando assim que haja propagação desordenada dos ruídos e também fazendo com que os demais circuitos suportem perturbações.
CURIOSIDADE: Existem Ensaios Laboratoriais que verificam se tais equipamentos possuem filtros apropriados para evitar que perturbações eletromagnéticas se dissipem pela linha de alimentação e comunicação de dados. Quando se trata de geração de perturbação para além do âmbito do veículo, também existe regulamentação. Atualmente, no exterior, existe a Norma CISPR 25 e CISPR 12, segundo a qual o Veículo é submetido a uma faixa de frequência entre 100 kHz e 2650 MHz, com um Campo elétrico de 140 V/m. Esta é a pior situação real possível, portanto executa-se este teste, que inclusive é aplicado em Veículos Militares.

OBSERVAÇÃO: Para entender o texto adiante deste parágrafo, o aconselho a ler os artigos sobre Condutores e Isolantes (CLIQUE AQUI! e CLIQUE AQUI!), Eletrodinâmica (CLIQUE AQUI! e CLIQUE AQUI!) e Resistores (CLIQUE AQUI! e CLIQUE AQUI!). Lá estão listadas diversas informações e tabelas relacionadas à:
-> Condutância e Resistência elétrica;
-> Tensão e Corrente elétrica;
-> Ligações em série e paralelo e alguns cálculos matemáticos;
-> Rigidez dielétrica e influência de temperatura;
-> Materiais condutores, isolantes e semicondutores e exemplos de aplicações.
De básico, lembre-se que, quanto maior a resistência de um cabo, menos corrente elétrica flui, bem como menor é a geração de calor.
Em relação à Corrente Elétrica, essa origina linhas de Campo Magnético. Essas Linhas de Campo circulam sempre ao redor do fio cuja corrente está fluindo. Sobre este assunto, aconselho a leitura da série de artigos sobre Indutores, podendo começar CLICANDO AQUI!
Imaginemos que quanto maior a corrente circulante em um condutor, maior o número de linhas de campo, e consequentemente maior a possibilidade de tais linhas atingirem outros cabos condutores paralelos. E isso originaria o que chamamos de “corrente parasita”, perturbações “na vizinhança” causadas devido altas correntes em cabos próximos. É aí que entram os cabos de vela resistivos em substituição aos velhos e simples cabos de Cobre.
Cabos de vela resistivos
A construção de um cabo de vela vai muito além de um simples fio resistivo. A blindagem contra interferências requer um amplo conhecimento e estudo em cima da Ciência e Tecnologia dos Materiais, já que aqui são necessários borrachas e plásticos com alta resistência física, excelente rigidez dielétrica e capazes de suportarem temperaturas elevadas.
De início, precisamos saber que existem dois principais tipos de cabos de vela resistivos: O do tipo SC e o do tipo ST (também chamado de "cabo de vela supressivo").
Cabos de vela Resistivos SC
Instigue-se com o diagrama abaixo:

Diagrama 1 - Cabo de vela resistivo SC por dentro. Créditos: NGK
Agora vamos desvendar o que é exatamente cada camada:
→ A base para a produção de um cabo Resistivo do tipo SC é um resistente e fino feixe de fios de Fibra de Aramida, mais conhecido pelo nome comercial "Kevlar".

Imagem 4 - O Poli P-fenileno Tereftalamida (PPTA) tem vários usos!
→ Sob este fio de fibra, um revestimento de borracha (elastômero, para os mais íntimos) cujo fabricante que publicou o informativo não especificou a composição química, porém, nada que fuja das já conhecidas resinas de EPDM ou CSM.
→ Nesta camada de borracha, há a impregnação de partículas ferromagnéticas (pó de ferro puro ou Ferrite, por exemplo). Aqui entra um adendo de extrema relevância...
CURIOSIDADE: Lembra-te daquele anel de Ferrite colocado próximo das extremidades de cabos USB, VGA, DVI, HDMI, DisplayPort e etc? Situe-se vendo a imagem abaixo:

Imagem 5 - Cabo adaptador VGA para DVI analógico com os anéis de Ferrite próximo dos conectores
Pois bem, se num cabo que opera com baixissimas tensões e correntes faz-se necessário o uso de um pequeno pedaço de material ferromagnético para supressão de ruídos, num cabo de vela, que pode trabalhar com dezenas de kV, o "concentrador de linhas de campo" é colocado em toda a extensão do cabo. Outro fator que difere o método de blindagem de um cabo de vela é que aqui o Ferrite está presente no "miolo" do cabo, e não em seu entorno.
CURIOSIDADE: Para saber mais sobre o Ferrite, CLIQUE AQUI! Caso queira saber mais sobre o Pó de Ferro, CLIQUE AQUI!
→ Sob esta manta de borracha impregnada com material ferromagnético há o fio resistivo, composto geralmente de Níquel-Cromo-Ferro (também chamado de "Nicromo"), material também utilizado na confecção de pequenos resistores e potenciômetros. Este fio está disposto em forma de espiral, isto é, um enrolamento que se assemelha com o resistor de um chuveiro.
Diferente de um resistor, onde o núcleo é composto de cerâmica HVA, filme ou pó de Carbono, aqui temos um núcleo de borracha (com pó de Ferro ou Ferrite) e Fibra de Aramida.
Este fio resistivo pode estar enrolado no núcleo juntamente de pequenas fibras, que podem ser de Poliamida (PA), cuja função é servir de "amarração", isto é, manter o resistor firme na estrutura:

Imagem 6 - Note que o fio resistivo está no meio dos fios de fibra polimérica. Distingui-lo pode ser um pouco complicado :v
CURIOSIDADE: Não é algo comum, porém existe uso de borracha condutiva em substituição ao Nicromo. O uso de cargas de Grafite ou Negro de Fumo, por exemplo, é feito em combinação com o núcleo emborrachado, 'moldando' a resiustência elétrica de acordo com a necessidade. Mas isso é conteúdo mostrado no artigo sobre condutores e isolantes!
A resistência elétrica do cabo é dada em Ohms por metro (Ω/m). Como exemplo prático, podemos pegar os cabos de ignição do motor GM SPE/4 mostrado na foto de capa deste artigo. O cabo utilizado no projeto possui resistência elétrica na faixa de 16 kΩ/m. Cada cabo deste motor possui pouco mais de 14 cm de comprimento, tendo uma resistência de 1.12 kΩ. Ao medir o comprimento do fio resistivo, não se pode levar em conta as capas dos terminais. Observe a imagem abaixo:

Imagem 7 - Como saber o comprimento do fio resistivo de um cabo de vela

Imagem 8 - Note as ponteiras do cabo
Note que, apesar de que não devemos levar em conta a capa dos terminais para calcular sua resistência, o cabo de vela é mais longo - principalmente no lado do 'cachimbo' -, inclusive suas pontas ficando dobradas na crimpagem dos conectores:
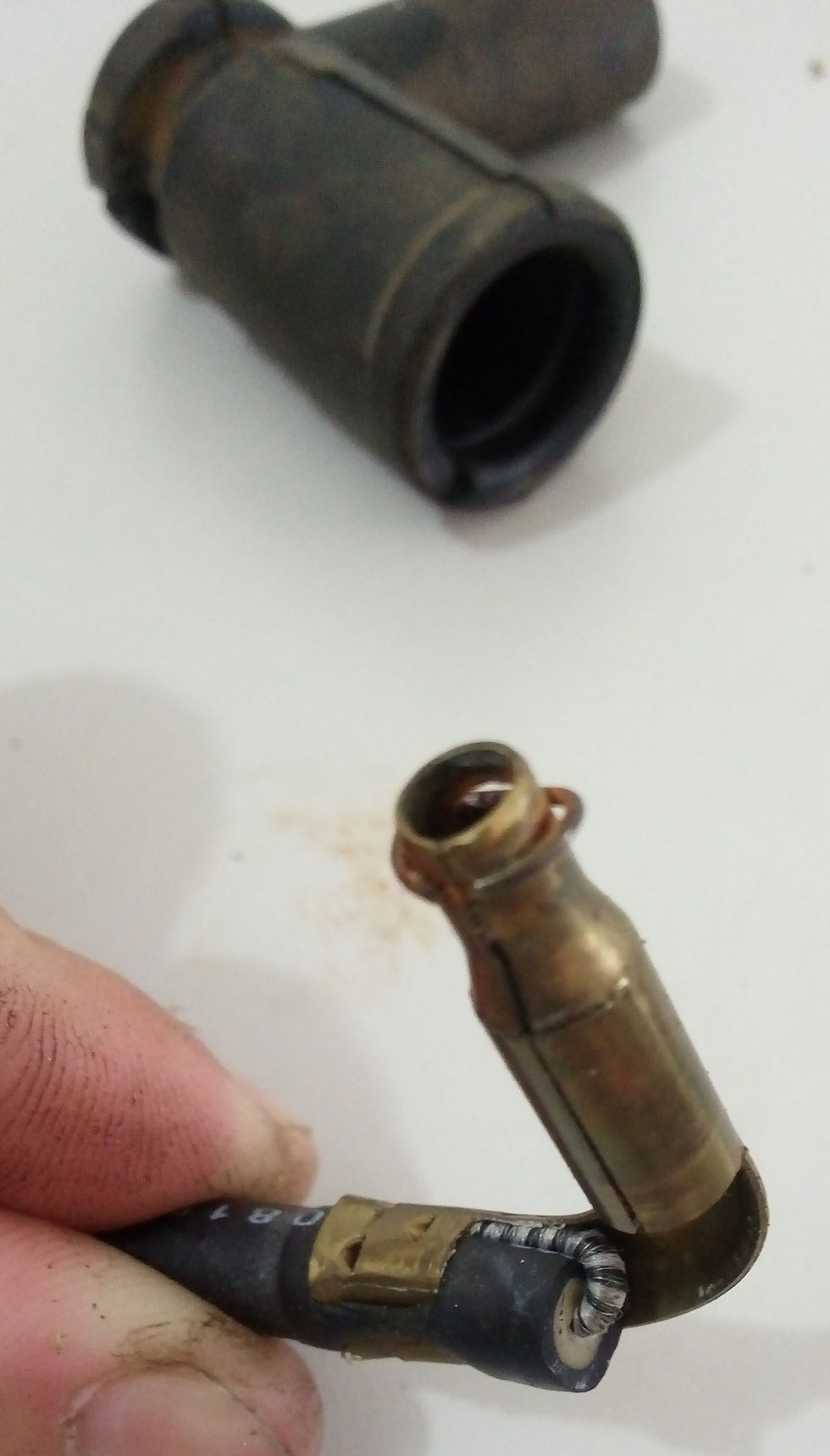
Imagem 9 - Os cabos de vela são mais longos do que parecem externamente
→ Perceba um revestimento branco entre o enrolamento e a capa preta externa do cabo. Aqui temos uma camada com excelente rigidez dielétrica formada por elastômero de Etileno-Propileno-Dieno-Metileno (abreviado EPDM).
Para os cabos cujo revestimento superficial seja borracha de Silicone, há uma manta de lã de vidro em conjunto com o EPDM. Aqui vai outra curiosidade relevante...
CURIOSIDADE: Alguns cabos de dados, como por exemplo cabos pra interface USB também podem fazer uso de algum outro composto com base em Etileno, sendo bem comum o polímero de Polietileno em sua forma espumada (FPE), que o torna mais flexível mesmo sendo um plástico. O uso da borracha EPDM em cabos de velas se dá por sua maior resistência, elasticidade e flexibilidade, bem como a já dita rigidez dielétrica, já que ele está em contato direto com a espiral de Nicromo.
→ Por último e não menos importante, o revestimento superficial do cabo. É a manta que vai o proteger das intempéries, podendo ser feita de Policloreto de Vinila (PVC) quando se trata de produtos mais baratos e menos duráveis, elastômero de Polietileno Cloro Sulfonado (CSM - material mais comum de se encontrar) e borracha de Silicone (Q - Mais cara devido ter durabilidade maior).
O Silicone é mais resistente ao calor, bem como a óleos e graxas. Abaixo, a imagem de um cabo de vela genuíno da linha FIAT FireEVO, cuja manta é feita em CSM:

Imagem 10 - Perceba o 'cachimbo', isto é, capa do terminal que se encaixa na vela. Ele também possui a mesma composição em CSM.
CURIOSIDADE: O PVC não possui muita resistência ao calor, tanto que quando se trata de conduítes corrugados utilizados no chicote elétrico do cofre do motor, os mais duráveis são aqueles feitos em Poliamida (PA) e que vem de fábrica com o veículo. Geralmente o que se encontra no mercado de reposição alternativo são conduítes corrugados feitos em PVC, com resistência pouco acima da temperatura de trabalho do motor (cerca de 100°C, pra ser mais exato), tendo uma durabilidade de poucos anos. O que muitos fazem é utilizar a famosa "malha náutica", um tecido de polímero PET que suporta temperaturas na casa dos 150°C.
A fabricante Bosch lista também a borracha EPDM como revestimento do cabo de vela. Observe parte de um folder do fabricante:

Folder 1 - Especificações do revestimento dos cabos de vela fabricados pela Bosch
CURIOSIDADE: Para saber mais detalhes sobre elastômeros de Silicone (Q), de NBR e EPDM, CLIQUE AQUI e leia o texto detalhando tais materiais. Para saber mais sobre Kevlar, PVC, bem como outros tipos de polímeros, CLIQUE AQUI!
Cabos de vela Resistivo ST
Os cabos de vela resistivos do tipo ST também são conhecidos como "cabos supressivos". Sua construção é mista, isto é, temos um cabo com fio de condutor (por exemplo Cobre ou Alumínio) e junto de seus terminais um resistor de Nicromo, como mostram os diagramas abaixo:

Diagrama 2 - Cabos de vela Supressivos - Crédito: Bosch
Em resumo:
→ 1 e 4: Referem-se a capa de isolação, isto é, o famoso "cachimbo", que neste caso pode ser feito de Silicone, CSM, PVC ou borracha EPDM, esta última citada em documentos da Bosch;
→ 3 e 4: Terminais de latão crimpado, melhorando a fixação dos materiais que compõem o cabo;
→ Perceba a existência de uma abraçadeira metálica ao redor da capa de isolação. Ela está ali pra fazer uma blindagem metálica contra interferências ao redor do "cachimbo" e é comum em muitos cabos de vela. Em resumo, esta "abraçadeira" nada mais é que um protetor "anti-EMI" (Eletromagnetic Interference);
→ O fio condutor pode ser Cobre ou Alumínio, e ao seu redor o mesmo revestimento descrito lá no início: Elastômero de EPDM com revestimento superficial de PVC, CSM, Q ou EPDM, como foi mostrado no Folder 1.
O revestimento dos terminais
→ Os terminais dos cabos de vela também possuem uma capa chamada popularmente de 'cachimbo' feita com o mesmo material isolante do cabo, ou seja, Silicone, CSM, EPDM ou PVC. Na confecção dos terminais, em geral, é utilizado ligas de latão (Cobre + Zinco, podendo ter outros elementos em quantidade menor, bem como galvanização com Estanho para inibir a oxidação do Cobre) e muito raramente Cobre puro galvanizado, porém, estes últimos encarecendo o valor final do produto.

Imagem 11 - Os conectores dos cabos de vela
Em muitos projetos, como o caso dos motores VHCE da GM, a extremidade do cabo que é encaixada na vela possui, além de um revestimento metálico tubular "anti-EMI" (também chamado de anel ou braçadeira), uma pequena mola que faz parte do sistema de encaixe e retenção. Essa mola é a ponte de ligação entre o anel anti-EMI e a carcaça do cabeçote (aterramento). Veja a imagem abaixo:
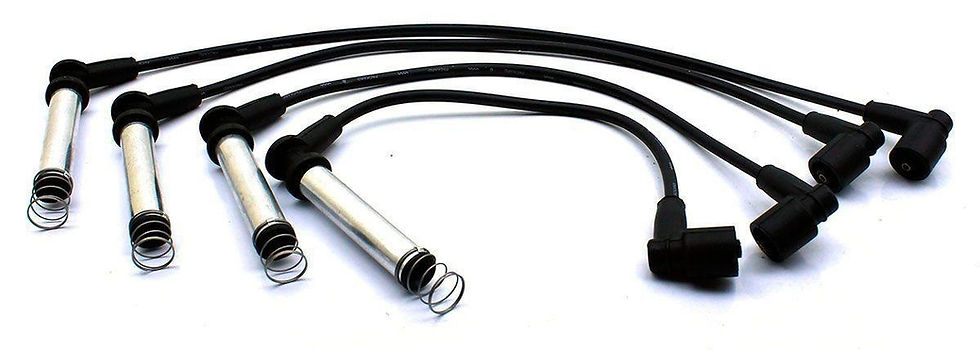
Imagem 12 - Cabo de vela da linha GM VHCE
Na imagem acima podemos notar outro fator importante: Em muitos projetos os cabos de vela costumam ter comprimentos diferentes, sendo que as velas mais próximas da bobina requerem cabos mais curtos e as mais distantes cabos mais longos. No entanto, TODOS os cabos do conjunto devem possuir a mesma resistência elétrica. Ou seja, para cada comprimento, há uma especificação diferente para o fio de Nicromo afim de manter todos eles com características elétricas idênticas.
Na Tabela seguinte, uma amostra retirada de um catálogo da MTA Automotive, com modelos de terminais de cabos de vela, sendo destacado o item "1", indicado como um resistor de fio enrolado com capa PBT-GF20 (Polibutileno Tereftalato com 20% de FV) para cabos supressivos. Os outros dois itens são terminais de liga de latão (Cobre + Zinco) envoltos em capa de EPDM ou PVC:

Tabela 1 - Os terminais dos cabos de vela são em latão na grande maioria dos projetos
E quando a bobina é do tipo "canetão"?
Neste caso também há cabo de vela!
Quando o motor possui uma bobina "canetão", o cabo é simplesmente a ponte de conexão do "canetão" com a vela. Ele é bem mais curto (óbvio), feito geralmente com um resistor de Nicromo (igual um cabo de vela comum) e com terminais de conexão em latão. Já o revestimento é o mesmo utilizado no restante da carcaça, que pode ser PBT-GF30, PET-GF30 ou MVQ (sim, existem bobinas "canetão" revestidas com borracha de Silicone), por exemplo.
Veja abaixo a bobina de ignição Mopar-Eldor de cód. 55267998, utilizada pela FIAT nos motores FIREFly:

Imagem 13 - Bobinas do tipo "canetão" para linha FIREfly da FIAT
Perceba que na parte em que estão escritas as informações do fabricante Mopar-Eldor, a textura preto-liso indica que há um preenchimento de poliepóxido. Se removesse este preenchimento, sobrará apenas o núcleo ferromagnético e seus enrolamentos, bem como um CI Driver (que é detalhado no artigo sobre bobinas de ignição) e o cabo de vela. Este preenchimento é uma camada isolante com alta rigidez dielétrica.
Agora, dois diagramas de bobinas do tipo canetão para entender onde se situa o cabo de vela:
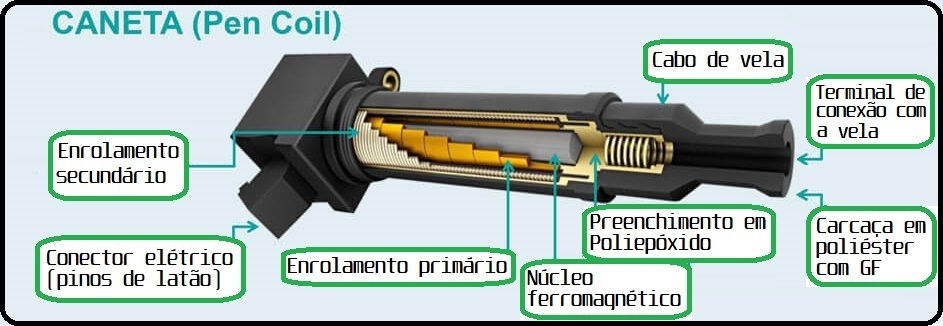
Diagrama 3 - Bobina do tipo "Pencil Coil", com um pequeno resistor de Nicromo antes do terminal de conexão da vela

Diagrama 4 - Bobina do tipo "Top Coil", com um pequeno resistor de Nicromo no corpo tubular. É a arquitetura utilizada na bobina Mopar-Eldor da Imagem 8
Apesar do caminho entre a bobina e a vela ser curto, também existe a formação de ruído que pode interferir em outros sistemas eletrônicos do veículo. Em algumas bobinas há um anel metálico ao redor do corpo, servindo como "escudo", ou melhor dizendo, blindagem anti-EMI.
Para saber mais sobre bobinas de ignição, CLIQUE AQUI!

Aqui coloco alguns detalhes que complementam o assunto principal.
A degradação dos cabos, velas e bobinas
É muito comum a degradação dos cabos de vela e até das bobinas em decorrência de velas desgastadas.
Quando há degradação nos eletrodos das velas, a resistência elétrica para formação da centelha se acentua, ou seja, aquela tensão aplicada entre os eletrodos poderá não ser suficiente para haver êxito na ionização da mistura A/C. No entanto, mesmo os cabos possuindo um isolamento demasiado grande, esta corrente que não 'circulou' através dos eletrodos pode pegar um outro caminho com menos resistência. Este caminho com menos resistência pode ser um ponto do cabo que esteja apoiado, isto é, encostado em um objeto 'aterrado', podendo ser por exemplo alguma parte metálica do motor. Isto pode tornar-se pior caso as camadas de isolamento do cabo estiverem degradadas, ou seja, ressecadas e com trincas, fissuras.
Por isso, vale a dica: Mesmo que os cabos de vela estiverem em ótimo estado de conservação, não se deve toca-los quando o veículo estiver ligado, tampouco toca-los se estiverem degradados. Se em bom estado há um leve risco de choque-elétrico, em mau estado de conservação há um baita risco!
CURIOSIDADE: Pelos eletrodos estarem desgastados, a alta resistência, além de gerar dificuldades de ignição, vai causar sobrecargas naquele que está gerando a alta tensão, ou seja, na bobina. Neste caso, a bobina tende a superaquecer (o cabo de vela também), o que pode resultar no rompimento de um enrolamento por incapacidade de dissipar tanto calor, inutilizando o componente.
Estendendo a explicação acima, podemos introduzir o fenômeno chamado de "flash over" no assunto.
Enquanto o motor está funcionado, no escuro, as vezes é possível notar uma luz pálida presente em torno do cabo de alta tensão e na superfície do isolador da vela de ignição. Este fenômeno é conhecido como "descarga Corona" ou "efeito Corona", e acontece por haver ionização em função da quebra da rigidez dielétrica do ar ao ser aplicado uma alta diferença de potencial. Se o ar está altamente ionizado, ocorre uma descarga parcial, resultando numa pálida luz azul.

Imagem 14 - O efeito corona. Cedido por: NGK
O efeito Corona ocorre com umidade, ocorre quando a superfície do isolador da vela está sujo ou quando há fissuras nos revestimentos dos cabos de vela (esses fatores provocam diminuição da resistência elétrica e um possível caminho para fluxo de corrente). Tem efeito mínimo no desempenho da vela, exceto quando a descarga provoca curto-circuito com uma parte metálica próxima (Podendo ser a própria carcaça do cabeçote), permitindo a formação do arco voltaico (flash over). Este arco provoca falhas de ignição, bem como danos irreversíveis no local onde ocorreu, isto é, no isolador da vela, nos revestimentos isolantes do cabo de vela ou na carcaça da bobina de ignição.
Se quiser entender melhor o efeito Corona, há um artigo sobre capacitores aqui do HC que cita-o também. Para lê-lo, basta CLICAR AQUI!
Para saber mais sobre a construção, o funcionamento e o desgaste das velas de ignição, CLIQUE AQUI!
O chaveamento pelo polo negativo
Perceba que em todos os tipos de cabo de vela há apenas um fio para a passagem de energia, sendo este é o polo positivo do circuito. O polo negativo é a própria carcaça do veículo, incluindo motor, câmbio e todos os periféricos que forem metálicos.
As velas de ignição, como sabemos, possuem dois eletrodos para a geração da centelha, sendo um deles ligado ao cabo de vela (positivo) e o outro ligado diretamente à carcaça da vela, que por sua vez é parafusada no cabeçote do motor.
Com base nos dois exemplos dados acima, podemos expandir a linha de raciocínio.
A maioria dos Especialistas fala sobre o procedimento correto para o desligamento da bateria, porém talvez se esqueçam de citarem o motivo pelo qual devemos seguir isso. Ao desconectar uma Bateria:
1. Soltar o borne Negativo;
2. Logo após, soltar o borne Positivo da bateria.
Ao conectar uma Bateria:
1. Prender o borne Positivo;
2. Prender o borne Negativo.
Essa ordem tem uma justificativa, e tem a ver com geração de Ruídos na Linha de Alimentação. Qualquer desconexão ou conexão tende a gerar um impulso de tensão e corrente. Ao “fecharmos” um circuito pelo borne negativo, estamos propiciando que tais ruídos façam seu trajeto no sentido normal. Uma desconexão ou conexão contrária ocasionará um impulso de tensão em sentido contrário, e tal distúrbio tenderá a se alastrar por toda rede de alimentação. Mas o que isto tem a ver com o assunto?
É justamente por este motivo que o chaveamento dos circuitos é feito pelo polo negativo, isto é, com sinal de polaridade negativa. Assim se evita a criação de ainda mais interferência dentro do próprio sistema.
OBSERVAÇÃO: Como dito anteriormente, o aterramento do circuito é toda a estrutura do veículo, isto é, qualquer parte metálica. Ele também é chamado no âmbito da mecânica e elétrica automotiva de "massa", porém, também é conhecido como terra ou ponto de potencial nulo, ou seja, aqui aterramento e polo negativo se confundem. Enfim, o real sentido da corrente elétrica é fluir do polo negativo (onde há excesso de elétrons) para o positivo (onde há falta de elétrons).

Com este conteúdo, temos mais um exemplo de uso dos resistores na indústria, bem como de materiais isolantes para a construção de sistemas eletrônicos. Com a popularização dos carros elétricos, os cabos de vela ficarão no passado, no entanto, o uso de altas tensões nestes veículos também exige condutores com características anti-EMI e isolamento elétrico de alta qualidade. Mas isto é conteúdo pra outra publicação!
E este foi mais um grande conteúdo do Hardware Central. Reunimos informações sobre eletrônica, química e CTM num só texto!
Se restou alguma dúvida, é só mandar um e-mail para hardwarecentrallr@gmail.com ou mande uma mensagem pelo Facebook. Se você gostou, é só curtir e compartilhar.
FONTES e CRÉDITOS
Texto: Leonardo Ritter
Imagens e Diagramas: Leonardo Ritter; NGK, Bosch; Google Imagens.
Referências: Livro "Eletrônica para Autodidatas, Estudantes e Técnicos"; Site dos fabricantes NGK e Bosch; Catálogo da MTA Automotive; Doutor-IE; Wikipedia (Somente artigos com fontes verificadas!).
Última atualização: 28 de Maio de 2023.
Comments