CTM: Borracha e Plástico - O que são? (Parte 2)
- Drano Rauteon
- 31 de mar. de 2021
- 29 min de leitura
Atualizado: 12 de jul.
Pra nós, basta olhar pra um objeto e dizer que ele possui plástico, borracha e ou metal em sua composição, mas não é bem assim que as coisas funcionam.
Plástico não é “tudo igual”, assim como a borracha e o metal também não são. É comum as pessoas classificarem a qualidade de um produto de acordo com essas terminologias, porém, devemos saber que há centenas de polímeros diferentes, que proporcionam milhares de combinações, isto é, compósitos, que permitem agregar características de diferentes materiais e criar produtos de alta qualidade. É o que ocorre com correias, que podem ser feitas de PA66-HNBR-GF-AF, de retentores que são feitos de PTFE ou FPM, de peças de motores e veículos feitas em PA66-GF ou PPGF, calços, coxins e batentes feitos em TPU, de dielétricos de capacitores feitos em PP, PE, PC e até polímeros semicondutores PPy e PEDT.
Mas para sabermos definir a qualidade de um produto, precisamos conhecer as combinações destes materiais, as qualidades e defeitos que cada um possui e a vantagem e desvantagem de utiliza-los. Também é necessário saber que há produtos iguais (que podem ser aplicados no mesmo sistema), todavia, feitos de materiais diferentes e com diferenças de preços gritantes, como é o caso de retentores. Um retentor de PTFE ou FPM possui uma durabilidade demasiadamente alta, entretanto, seus preços destoam das outras tecnologias mais defasadas, e essa falta de conhecimento do povo sobre as justificativas do preço alto fazem com que a maioria opte pelo mais barato achando que é “tudo a mesma coisa”.
Outra coisa fácil de se ver na população leiga e até entre profissionais desses ramos é que muitos não conhecem de fato o produto que estão utilizando (ou pelo menos insistem em utilizar termos errôneos). Um bom exemplo são as velhas juntas de vedação estáticas de cabeçotes de motores a combustão interna, que antigamente eram baseadas em Fibra de Amianto e que, pela legislação moderna, foram substituídas por Fibra de Vidro e ou Fibra de Aramida, porém, até hoje são conhecidas por todos como “juntas de amianto” ou “juntas de papelão de amianto”.
Nesta série de artigos, com a concatenação de informações selecionadas em vários sites, escritas por vários autores, trago a explicação resumida sobre Plásticos e Borrachas e exemplos de vários materiais compósitos que são utilizados amplamente pela indústria química, automobilística, eletrônica e diversas outras, porém, com enfoque na eletrônica e mecânica.

Continuando o capítulo anterior, este artigo tratará da borracha, outro material essencial nos dias atuais.
Borrachas são resinas que podem ser de origem natural ou sintética. Independente da origem as borrachas são elásticas, ou seja, elastômeros. Tanto a borracha quanto o plástico são feitos de polímeros. O que difere uma borracha de um plástico é seu comportamento mecânico, ou seja, a elasticidade. Para completar, tanto a borracha sintética quanto o plástico também podem ser denominadas resinas.

O primeiro material conhecido como borracha (“caoutchouc” derivado da palavra índia “caa-o-chu”) é o poliisopreno recolhido da seiva da árvore Hevea Brasiliensis (as popularmente chamadas seringueiras), o látex, sendo então chamado de borracha natural (NR). A borracha natural pode reagir com o Enxofre a temperaturas elevadas para formar reticulações, ocorrendo a transformação de um estado pegajoso e fundamentalmente plástico num estado elástico.
A borracha natural é um cis-1,4-poliisopreno, apresentando uma longa cadeia polimérica linear com unidades isoprénicas (C5 H8) repetitivas e com densidade aproximadamente igual a 0,93 a 20 °C, obtido por coagulação do látex. Os graus de qualidade mais elevados são obtidos através da coagulação por acidificação, sob condições fabris cuidadosamente controladas.
O isopreno é um sinônimo comum para o composto químico 2-metil-1,3 butadieno.
A borracha natural comercial tem uma pequena quantidade, 4 a 9%, de outros constituintes. Destes, os mais importantes são os antioxidantes naturais e ativadores de vulcanização representados pelas proteínas e ácidos graxos.
CURIOSIDADE: O látex é produzido em muitas espécies vegetais tropicais, porém, praticamente toda a produção mundial de borracha natural vem da extração de látex da seringueira.
Através de incisões no caule da já dita árvore, o líquido branco escorre, sendo coletado em tigelas e devendo ser recolhido com frequência a fim de evitar contaminação e putrefação.
O polímero da borracha é um polímero de adição, conhecido como poli-isopreno, pois é formado pela adição de 1,4 de monômeros de isopreno (metilbut-1,3-dieno):

Fórmula estrutural 1
Essa reação está aqui de um modo simplificado, pois nas árvores elas são bem mais complexas e necessitam de enzimas atuando como catalisadores. O valor de "n" na fórmula do poli-isopreno acima é na ordem de 5000 e a borracha natural é formada por cerca de 35% desse polímero. Veja a macromolécula do poli-isopreno abaixo:

Imagem 1
Na indústria da borracha, desde que T. Hancock e Charles Goodyear obtiveram, em 1843 e 1844, as primeiras placas de borracha natural, muito se avançou. Essas placas representam o começo da produção de artigos de borracha e da formulação de compostos. Na maioria dos casos, os compostos de borracha baseados em borracha natural ou sintética, necessitam de serem vulcanizados com Enxofre, peróxidos, óxidos metálicos ou combinações dos mesmos. Outros produtos químicos são também necessários para se obter ou melhorar propriedades físicas, químicas ou térmicas específicas.
CURIOSIDADE: A borracha natural foi a primeira e única borracha a ser utilizada até 1927, sendo o seu interesse atual não simplesmente histórico, mas sim devido ao seu potencial técnico.
Classificação da Borracha Natural (NR)
Podemos classificar a borracha natural em três grandes grupos:
Graus convencionais
→ “Ribbed Smoke Sheets” (RSS);
→ “Air-Dried Sheets”;
→ “Pale Crepe”;
→ “Sole Crepes”;
→ e os “Brown and Blanket Crepes”.
Borrachas tecnicamente especificadas (TSR)
Foram introduzidos pela primeira vez no mercado em 1965 pela Malásia como “Standard Malaysian Rubber” (SMR). Esta adesão pela Malásia à normalização foi posteriormente seguida por outros países produtores, tais como a Indonésia com a “Standard Indonesian Rubber” (SIR).
Os graus mais comuns dentro dos TSR são:
→ “SMR L” de cor muito clara;
→ “SMR CV” com viscosidade estabilizada;
→ “SMR WF” similar a SMR L (porém de cor mais escura);
→ “SMR GP” de uso geral (mas com viscosidade estabilizada e adequada para uso em pneus);
→ “TSR 5” feita de látex usando o mesmo processo de obtenção do SMR L, mas sem tratamento com Metabissulfito de Sódio;
→ "TSR 10";
→ "TSR 20";
→ e "TSR 50".
Borrachas tecnicamente classificadas (TCR)
Podemos considerar a:
→ Borracha Natural Extendida com Óleo (OENR), que contém cerca de 20% a 30% de um óleo de processamento aromático ou naftênico;
→ Borracha Natural Desproteinizada (DPNR);
→ Borrachas de Superior Processamento (SP);
→ Borracha Natural Epoxidada (ENR);
→ e Borracha Natural Termoplástica (TPNR, da classe dos Elastômeros termoplásticos).
Para além dos graus de borracha natural provenientes da Malásia e da Indonésia e classificados de acordo com as especificações do país de origem, SMR e SIR, respectivamente, encontram-se no mercado outros graus, tais como:
→ TTR, da Tailândia;
→ SSR, de Singapura;
→ NSR, da Nigéria;
→ CAM, de Camarões;
→ GHA, do Ghana;
→ GAB, do Gabão;
→ LIB, da Libéria;
→ SPR, das Filipinas;
→ PNG CR, da Papua Nova Guiné;
→ SLR, do Sri Lanka;
→ SVR, do Vietnam;
→ e CSR, da China.

Dentro desta classificação existem as borrachas orgânicas e as inorgânicas.
Borrachas Orgânicas
As borrachas sintéticas são polímeros diênicos sintetizados, como o polibutadieno e o policloropreno. Imitando a reação que ocorre nas árvores da seringueira, os cientistas passaram a realizar reações de polimerização de adição de compostos diênicos, produzindo vários tipos de borrachas sintéticas. Dependendo do tipo de monômero que se usa para produzir o polímero, conseguem-se borrachas com diferentes propriedades.
Atualmente, as borrachas sintéticas são mais utilizadas do que a borracha natural. Tanto a natural quanto as sintéticas são consideradas elastômeros, isto é, substâncias que, quando são submetidas à tensão passam de rearranjos desordenados a arranjos lineares, de maneira reversível.
As borrachas sintéticas mais comuns atualmente são as obtidas por meio da polimerização do acetileno (buta-1,3-dieno), que forma o polibutadieno, e a partir do cloropreno (2-clorobut-1,3-dieno), que produz o policloropreno:

Fórmula estrutural 2
CURIOSIDADE: O policloropreno foi originalmente introduzido no mercado pela química norte americana Du Pont sob o nome comercial Duprene como uma borracha sintética com boa resistência ao óleo e ao ozônio. Posteriormente, a DuPont apresentou novos tipos de CR com melhores características de laboração e vulcanização sob o nome comercial Neoprene.
Parte da borracha usada nos pneus é sintética, conhecida como BuNa-S, sendo formada pelo eritreno (but-1,3-dieno) e pelo estireno (vinilbenzeno), que em inglês escreve-se “styrene”, por isso, o “S” no final. O “Na” também vem da atuação do sódio (Na – do latim Natrium) como catalisador:

Fórmula estrutural 3
CURIOSIDADE: BuNa-S é conhecido atualmente como SBR (Borracha de Butadieno Estireno). Foi elaborada na Alemanha na década de 1930 com o nome de BuNa-S e posteriormente estudada nos Estados Unidos durante a 2ª Guerra Mundial, porém, era chamada de GRS (Government Rubber-Styrene).
A BuNa-S é um copolímero, sendo formada pela adição de diferentes monômeros. Outros exemplos de borrachas sintéticas que também são copolímeros é a Buna-N, que é usada em revestimentos de tanques de gasolina, de mangueiras e em gaxetas.
O BuNa-N é formado pelo eritreno (but-1,3-dieno), de onde vem o prefixo “bu”, e pela acrilonitrila, de onde vem um grupo Nitrilo e, por isso, o “N” no final. Já o “Na” vem do sódio, que atua como catalisador na reação de polimerização desse copolímero:

Fórmula estrutural 4
CURIOSIDADE: O BuNa-N é conhecido no mercado como NBR (Borracha nitrílica). Foi no ano de 1931 que apareceu pela primeira vez uma referência à NBR num documento relativo a uma patente de origem francesa abrangendo a polimerização de butadieno e acrilonitrilo.
A produção de NBR em escala industrial começou em 1934 na cidade alemã de Leverkusen, tendo o primeiro tipo de NBR aparecido no mercado sob o nome de BuNa-N e, mais tarde, como PerBuNaN-N.
Já a borracha sintética ABS, que entre suas utilidades estão a produção de pneus, carcaças de aparelhos elétricos e eletrônicos e em embalagens, é formado pela união de três monômeros: acrilonitrila (A), but-1,3-dieno (B) e estireno (S, do inglês “Styrene”):

Fórmula estrutural 5
Borrachas Inorgânicas
Quando o Polímero não possui átomos de Carbono na cadeia principal ele é considerado uma resina inorgânica, como é o caso do Silicone.
O Silício pertence à mesma família do Carbono na Tabela Periódica, vindo no período logo após o do Carbono, sendo assim o 'Si' apresenta propriedades semelhantes às do 'C' e, portanto, pode se ligar a grupos orgânicos.
CURIOSIDADE: Frederick Stanley Kipping (1863 ~ 1949) é considerado o fundador da química do silicone. É por vezes referido que Berzeluis, em 1823, conseguiu isolar o Silício e juntamente com Wohler conseguiram sintetizar os primeiros clorosilanos.
Usando a “Grignard Chemistry” desenvolvida por Kipping, Dr. Eugene G. Rochow, da “General Electric Laboratories”, começou a trabalhar nos metilsilicones em 1938, tendo descoberto em 1940 o processo direto para a produção dos metilclorosilanos processo que envolve a reação do cloreto de metilo com Silício (obtido este através da redução do SiO2) na presença de um catalizador de Cobre, sendo o principal produto da reação o dimetildiclorosilano que após purificação é hidrolizado obtendo-se uma mistura de polímeros lineares e cíclicos de baixo peso molecular. O hidrolizado era originalmente polimerizado com um catalizador ácido, sendo atualmente removidos os cíclicos numa etapa adicional de purificação. Este processo tornou os metilclorosilanos disponíveis a um custo razoável e tornou possível a atual indústria de Silicone.
Pulando mais pra frente na história, em 1958 a Rhône Poulenc registrou a sua primeira patente. Era um polímero de silicone que vulcanizava com a humidade ambiente. Foi aí que nasceu os populares vedantes conhecidos, ainda hoje, pelo seu nome francês "mastics", ou em bom português "cola de silicone".
O Silicone tem como característica principal a cadeia polimérica de átomos de Silício e Oxigênio, em que os átomos de Silício transportam dois radicais orgânicos, preferencialmente radicais metilo. As propriedades especiais da borracha de Silicone estão relacionadas com a presença de pequenas quantidades de radicais vinilo, fenilo ou fluoroalquilo. Os vulcanizados de borracha de silicone distinguem-se pela:
-> Sua excepcional resistência ao calor;
-> Estabilidade a baixa temperatura
-> Flexibilidade a baixa temperatura
-> Excelente resistência ao Oxigénio, ozônio e radiação UV;
-> Boa rigidez dielétrica.
A borracha de Silicone tem uma cadeia polimérica que contém átomos de Silício e de Oxigénio, sendo as valências livres do átomo de Si neutralizadas pelos radicais orgânicos "R" como mostra a figura abaixo:

Fórmula estrutural 6
Existem vários tipos de borracha de silicone, sendo os mais comuns listados abaixo.
-> Borracha MQ: Foi o primeiro a ser produzido pela indústria. A borracha de Silicone MQ é um polimetilsiloxano que contém radicais metilo. Veja a fórmula abaixo:

Fórmula estrutural 7
-> Borracha VMQ: Com a introdução de alguns radicais vinilo na molécula de MQ obtemos a borracha metil-vinil-siliconica (VMQ), que vulcaniza mais rapidamente que a borracha MQ e cujos vulcanizados têm melhores características. Por este motivo a borracha de silicone mais utilizada é a borracha VMQ. Veja a fórmula abaixo:
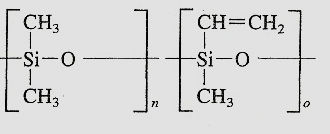
Fórmula estrutural 8
-> Borracha PMQ: A borracha MQ tende a se tornar rígida em temperaturas inferiores a -60 °C. Se introduzirmos na molécula de MQ ou na molécula de VMQ alguns radicais fenilo, obtemos a borracha metil-fenil-siliconica (PMQ). Veja a fórmula abaixo:

Fórmula estrutural 9
-> Adicionando radicais vinilo na borracha PMQ temos a borracha metil-fenil-vinil-siliconica (PVMQ). Veja a figura abaixo:
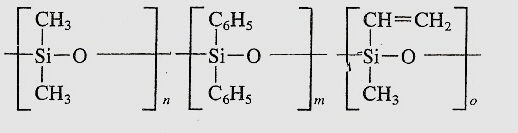
Fórmula estrutural 10
CURIOSIDADE: Borrachas de PMQ ou PVMQ apresentam uma excepcional resistência a baixa temperatura mas uma menor resistência ao inchamento.
-> Borracha FMQ: As borrachas de MQ apresentam bom comportamento em acetona e diésteres mas mau comportamento (inchamento a 200%) em hidrocarbonetos alifáticos e aromáticos. Substituindo na borracha MQ um radical metilo em cada átomo de Silício por um radical polar como o trifluorpropilo (-CH2CH2CF3), obtemos a borracha FMQ, que apresenta um inchamento reduzido (valores inferiores a 25%) nos hidrocarbonetos alifáticos e aromáticos, porém um aumento do inchamento em acetona e diésteres. Veja a figura abaixo:

Fórmula estrutural 11
CURIOSIDADE: As diferentes borrachas de Silicone são frequentemente designadas simplesmente por “Q”.

As borrachas, sejam naturais ou sintéticas possuem algumas propriedades que dificultam a sua utilização. Por exemplo, é comum das borrachas naturais tornarem-se duras e quebradiças no frio, enquanto no calor ficarem moles e pegajosas.
Por isso as borrachas precisam passar por um processo chamado de vulcanização, que foi descoberto em 1839 por Charles Goodyear. Trata-se da adição de Enxofre, que rompe as suas ligações duplas e forma pontes de Enxofre que ligam as cadeias laterais e tornam a histerese da borracha mais baixa (se ela for apertada, por exemplo, rapidamente ela irá voltar para seu formato original), baixa deformação permanente e grande elasticidade. Desse modo, a borracha pode ser usada para a fabricação de inúmeros produtos.
De forma resumida, a borracha vulcanizada possui mais resistência física e elasticidade do que a borracha “crua”.
Para ver mais sobre vulcanização de borrachas, acesse os PDFs abaixo:
Vulcanização com Enxofre:
Vulcanização sem Enxofre:
Mas o que seria a histerese da borracha?
Observe o gráfico de histerese abaixo:

Gráfico 1 - Curva de histerese da borracha
Antes de explicar o gráfico 1, é bom saber o que é resiliência da borracha. Esta propriedade é uma medida da aptidão da borracha para restituir, quando ocorre a recuperação elástica, a energia que lhe provocou a deformação. Quanto maior for a resiliência, maior é a quantidade de energia restituída. É habitual também dizer-se que é maior a “elasticidade” da borracha. Ou seja, se a borracha é pouco elástica, ao ser esticada além de seus limites ela dissipará a energia que provocou a deformação, permanecendo deformada então. Por este motivo que plásticos ao serem deformados não retornam ao seu formato normal, tendo uma elasticidade zero ou próxima de zero.
Se a borracha não retornar ao seu formato original é por que ela dissipou alguma quantidade de energia em forma de calor. Em outras palavras, quanto maior for a área entre a linha "esticada" e a linha "relaxada" do Gráfico 1, maior será a energia dissipada em forma de calor e menor será a elasticidade da borracha.
Em situações extremas, isto é, quando o componente de borracha não restitui praticamente nenhuma energia, a elevação de calor é tal, que conduz à sua destruição. Esta propriedade pode ser importante em muitas aplicações de natureza estática, mas é muito mais importante em aplicações de natureza dinâmica e especialmente nos casos de tensões dinâmicas de elevada frequência, em que a acumulação de energia observada ao fim de um certo número de ciclos pode também conduzir à destruição do componente.
CURIOSIDADE: Sistemas mecânicos que já estão a muito tempo em funcionamento sem manutenção, com borrachas de absorção de vibração e impactos expostas a intempéries (umidade, calor, poeira, óleos e outros líquidos) vão aos poucos perdendo a resiliência, abrindo fissuras e largando fragmentos até sucumbirem de vez e se romperem. É exatamente o que acontece com coxins de motores, buchas e coxins de suspensão dos veículos.
Aonde que entra a vulcanização nesse processo?
A vulcanização é a quebra de ligações químicas do composto com a criação de pontes de enxofre (ou outro material apropriado) para reduzir a histerese do elastômero e melhorar sua consistência em ampla faixa de temperatura. Basicamente a vulcanização faz pontes que aumentam as ligações de cadeias de átomos.
Em outras palavras, a vulcanização consegue diminuir ou aumentar a histerese da borracha, dando ou melhorando características elásticas dentro de uma faixa de temperatura específica de acordo com o polímero e os aditivos utilizados e também de acordo com a quantidade de agentes vulcanizantes adicionados no processo de produção. Veja o gráfico abaixo:

Gráfico 2 - Características do material de acordo com o grau de vulcanização

Mais informações sobre alguns dos principais compostos de borracha orgânicos.
CURIOSIDADE: Nos pneus dos veículos a borracha predomina, sendo 27% sintética orgânica e 14% natural. O negro de fumo constitui 28% da composição. Os derivados de petróleo (como por exemplo a Cera Parafínica ou Carbono Amorfo) e produtos químicos (como por exemplo Óxido de Zinco e Ácido Esteárico) respondem por 17%, o material metálico (ou aço) por 10% e o têxtil por 4%. Lembrando que há a adição de Enxofre como agente vulcanizador.
Os pneus de automóveis são projetados para suportar altas velocidades, enquanto os pneus de carga são fabricados de acordo com a massa que deverão sustentar. Com isso, a quantidade de borracha natural nos pneus de caminhões está em torno de 30%.
Já que o assunto é pneus e borrachas, acho um momento oportuno pra mostrar isso:

Imagem 2 - Créditos: Garagem do Bellote TV (You Tube)
A imagem acima é do pneu reserva do "Sueco voador", o icônico SAAB 900 Turbo S 16V AERO, trazido pela General Motors para testes em 1991 e que ficou por aqui, na mão de um colecionador.
→ Borracha sintética do tipo NBR (Borracha Nitrílo-Butadieno). A borracha nitrílica pertence à classe das borrachas especiais resistentes ao óleo e é um copolímero de butadieno e acrilonitrilo, sendo a polimerização feita por um processo de emulsão - assim como é feito o SBR -, podendo ser realizada a quente ou a frio, obtendo-se os denominados “hot nitriles” e “cold nitriles” conforme a temperatura é superior a 30 °C ou se situa entre 5 °C e 30 °C, respectivamente.
Os diferentes graus (ou tipos) de NBR distinguem-se pelo conteúdo em acrilonitrilo (abreviadamente ACN), o qual pode variar de uma forma geral de 18 a 51 % e também pela viscosidade.
Na produção de NBR, tal como no caso do SBR, existem muitos parâmetros que variando originam uma grande diversidade de graus comerciais disponíveis. Alguns desses parâmetros são:
→ Teor em acrilonitrilo que influencia diretamente a resistência ao óleo e à gasolina, bem como a flexibilidade a baixa temperatura;
→ Temperatura de polimerização que origina os “hot” ou “cold” nitrilos;
→ Modificador da cadeia que provoca diferenças na viscosidade Mooney e no processamento;
→ Estabilizador que origina diferenças na cor e na estabilidade durante a armazenagem;
→ Misturas com PVC que produzem os tipos de borracha conhecida como NBR/PVC.
Resumidamente, a borracha nitrílica (NBR) oferece um bom balanço entre a resistência a baixa temperatura (entre -10 °C e -50 °C), ao óleo, a combustíveis e aos solventes, resistência essa em função do teor em acrilonitrilo. Estas características combinadas com uma boa resistência a alta temperatura e à abrasão, tornam a borracha de NBR aconselhada para uma grande variedade de aplicações. Apresenta também boa resistência à fadiga dinâmica, baixa permeabilidade ao gás e a possibilidade de ser misturada com materiais polares como o PVC.
→ Borracha do tipo SBR (Borracha de Estireno Butadieno): Utilizada em solas de sapato, mangueiras, bastante utilizada na confecção de correias, sendo normalmente parte de um compósito.
A maior parte do SBR, cerca de 85 a 90%, é polimerizado por emulsão, sendo os restantes 10 a 15% polimerizados em solução.
Da mesma forma que ocorre com a borracha NBR, em função da temperatura de polimerização, a borracha obtida é classificada de “hot rubber” se a temperatura de polimerização é de cerca de 55 °C e de “cold rubber” se a temperatura de polimerização se situa entre 5 ~ 10 °C, possuindo esta última melhores características de laboração. Considerando o tipo de estabilizadores usados na polimerização, o SBR é classificado como "SBR manchante" (staining) e "SBR não manchante" (non-staining).
Existe também o SBR estendido com óleo (oil extended SBR), sendo o mais comum o que contém 25 a 50 partes em peso de plastificante sobre 100 partes de borracha, sendo este tipo de SBR o de mais fácil processamento. Os óleos usados podem ser aromático ou nafténico; o óleo parafínico não é utilizado porque não é suficientemente solúvel no SBR. Os tipos mais conhecidos de SBR extendido com óleo são o SBR 1712 (escuro) e o SBR 1778 (claro). Outras formas populares de SBR modificado são os “Masterbatches” feitos com óleo e negro de Carbono.
Os vulcanizados obtidos a partir da borracha SBR apresentam uma melhor resistência à abrasão do que a borracha natural (NR), assim como uma melhor resistência a altas temperaturas (100 °C) e ao envelhecimento, mas uma menor flexibilidade e elasticidade a baixas temperaturas (até cerca de -50 °C). No caso das temperaturas elevadas, os vulcanizados de SBR apresentam um endurecimento e não um amolecimento como acontece com os vulcanizados de borracha natural. A permeabilidade ao gás é elevada mas menor do que a dos vulcanizados de borracha natural enquanto que a resistência química é semelhante à da borracha natural.
→ Borracha de Policloropreno: Material utilizado na indústria textil e automobilística.
Se o cloropreno for polimerizado sem qualquer aditivo de modificação, o produto obtido é tão duro e insolúvel que é impossível de processar, tendo, portanto, que se decompor a cadeia do polímero para permitir pontos de clivagem. Os dois métodos usados para obter a processabilidade são:
-> o processo tipo tiurame ou modificado com Enxofre; -> Um processo sem Enxofre, modificação por Mercaptano.
Embora a resistência ao óleo das borrachas então existentes tenha sido melhorada com o aparecimento das borrachas nitrílicas, e a resistência ao ozônio com o aparecimento das borrachas EPT (terpolímero de etileno e propileno), a borracha de policloropreno continuou a ser bastante utilizada devido à boa combinação de propriedades e processabilidade apresentada.
A classificação do policloropreno foi feita considerando o grupo destinado ao fabrico de adesivos e o grupo para aplicação geral na indústria, subdividido este último em três famílias, a família G, a família W e a família T
-> Família G: Os graus mais típicos são o Neoprene GN, com pouca estabilidade enquanto matéria-prima, o Neoprene GNA e o Neoprene GT, estes com melhor resistência à cristalização, embora pequena;
-> Família W: Possuem melhor estabilidade de armazenagem e maior resistência à cristalização, fruto da modificação com mercaptano sofrida durante a polimerização. Têm também uma distribuição mais uniforme do peso molecular e necessitam normalmente de catalisadores orgânicos para que a vulcanização seja razoavelmente rápida. Os graus mais típicos são o Neoprene W, o Neoprene WHV e o Neoprene WK. O Neoprene WRT é o mais resistente à cristalização;
-> Família T: São mais comuns o Neoprene TW e o Neoprene TRT, ambos semelhantes ao Neoprene tipo W e contendo uma fração de polímero gel para melhorar o seu comportamento. São resistentes à cristalização e necessitam de catalisadores orgânicos.
→ Borracha sintética HNBR (Acrilonitrilo Butadieno Hidrogenado): Uma evolução do NBR descrito anteriormente.
A produção da borracha de Acrilonitrilo Butadieno Hidrogenado começa com a obtenção de um NBR pelo processo de polimerização por emulsão, sendo depois este polímero dissolvido num solvente apropriado. Após a dissolução estar completa, a adição de Hidrogênio gasoso em conjunto com um catalisador metálico sob uma determinada temperatura e pressão provoca uma hidrogenação seletiva, parcial ou completa, para produzir um polímero de nitrilo altamente saturado. A designação de HSN ("high satured nitrile") pela qual o HNBR é por vezes referido, tem neste fato a sua origem.
O solvente e o catalisador são depois recuperados e a fração restante seca, sendo o produto seco seguidamente embalado e empacotado. Os catalisadores adequados para serem usados em soluções aquosas podem ser complexos de Piridina-Cobalto ou complexos de Rádio, Rutínio, Iridio ou Paladio, sendo particularmente efetivo um catalizador baseado em metais de transição com um iodeto trivalente de Rádio.
Os diferentes tipos de HNBRs disponíveis no mercado abrangem uma gama de conteúdo em acrilonitrilo (ACN), de cerca de 17 a 50% e uma gama de viscosidades de 50 a aproximadamente 150 ML (1+4) a 100 °C, o que é bastante vantajoso, uma vez que é possível fazer a escolha de acordo com as propriedades pretendidas e de acordo com o processo de manufatura que vai ser usado (moldagem por compressão, injeção ou transferência ou processo de extrusão).
O teor em ACN determina aqui, tal como no caso da borracha de NBR, a resistência aos fluidos, a resistência química, e também o desempenho em baixa temperatura da seguinte forma:
Aumentando o teor em acrilonitrilo, diminui o aumento de volume do composto correspondente e melhora a resistência química, mas a flexibilidade a baixa temperatura fica mais pobre.
Igualmente importante é o nível de hidrogenação (grau de saturação) do HNBR já que, à medida que ele aumenta, melhoram a resistência ao calor, ao Ozônio e o desempenho em meios quimicamente agressivos (tais como óleos contendo aditivos do tipo amina), diminuindo, no entanto, a histerese dinâmica. Devemos igualmente referir que o nível de hidrogenação condiciona a escolha do tipo de sistema de vulcanização a ser utilizado.
Os HNBRs totalmente saturados têm uma excelente tensão de rotura, boa flexibilidade a baixa temperatura e muito boa resistência à abrasão. Após exposição à temperaturas elevadas, estes HNBRs retêm melhor as suas propriedades mecânicas do que, por exemplo, os vulcanizados de FKM. Apesar da sua menor resistência ao calor e maior aumento de volume após imersão em óleos quando comparado com o FKM, os HNBRs completamente saturados podem competir em várias aplicações, como ocorre no setor automotivo, onde retentores de válvulas são feitos de fluoelastômero, enquanto correias BIO são feitas com uma matriz de HNBR, e ambos podem passar toda a vida útil em contato com óleo e sob altas temperaturas tranquilamente.
Os tipos parcialmente insaturados apresentam um grau de saturação de 95%, ou seja, têm um conteúdo residual de dupla ligação de cerca de 5%, relativo ao conteúdo de dupla ligação da base NBR. Este nível de insaturação origina um bom balanço entre um sistema de vulcanizaço eficiente e uma boa resistência à compressão em baixas temperaturas. Os valores de resistência ao rasgamento e de alongamento na rotura são geralmente maiores dos que os obtidos com graus totalmente saturados vulcanizados com peróxido.
De acordo com o grau de hidrogenação, torna-se possível o equilbrio entre alta temperatura e resistência ao ambiente com propriedades dinâmicas
O HNBR insaturado reticulado com Enxofre não tem tão boa estabilidade ambiental como um HNBR completamente saturado, todavia, tem melhores propriedades dinâmicas.
CURIOSIDADE: As formulações de HNBR são elaboradas diferentemente das de NBR. Sendo a NBR uma borracha altamente insaturada, a vulcanização é, em principio, muitas vezes da mesma forma que a borracha natural ou o SBR. O HNBR ou é pouco insaturado ou não tem sequer nenhuma insaturação, o que influencia e condiciona não só a seleção dos agentes de vulcanização e dos agentes de proteção, como igualmente a escolha das cargas e dos plastificantes aplicados.
As formulações de HNBR contêm, habitualmente, para além do polímero, cargas minerais, plastificante, óxidos metálicos, agentes protetores, auxiliares de processamento, agentes de vulcanização e, eventualmente, coagentes.
Além dos Negros de Carbono, dos quais podemos referir especialmente o FEF, o MT, o GPF e o SRF, podemos também usar cargas brancas, que dão uma melhor resistência ao envelhecimento, entretanto, necessitarão - como é habitual - da adição de um ativador. Se houver necessidade de usar um plastificante, ele deve ser, preferencialmente, um éster de ácido sebácico ou de ácido trimetilico.
Os óxidos metálicos (que também são cargas brancas) aplicáveis são o Óxido de Magnésio e o Óxido de Zinco, enquanto os agentes protetores mais comuns são os derivados das difenilaminas (como o Vulkanox DDA e OCD), os TMQ (por exemplo Vulkanox HS), o metilbenzimidazole e o seu derivado mercapto (Vulkanox MB 2 e ZMB2), e como auxiliares de processamento há o Levapren EVM - que reduz o custo sem afetar a resistência ao envelhecimento -, cera de carnauba, cera de parafina ou ceras de Polietileno, ácido esteárico ou o estearato de Zinco, destinando-se estes dois últimos a melhorar a dispersão da carga branca - mas sendo somente efetivos com graus de HNBR parcialmente insaturados.
Propriedades dos Vulcanizados de HNBR
De uma forma geral, os vulcanizados de HNBR podem ser utilizados numa gama de temperaturas de -40 °C a 160 °C e apresentam:
→ Elevados valores de tensão de rotura;
→ Boa resistência à compressão, especialmente a alta temperatura;
→ Boa flexibilidade a baixa temperatura;
→ Excelente resistência ao Ozônio;
→ Boa resistência ao vapor;
→ Boa resistência a radiações ultravioleta;
→ Boa resistência química a óleos parafínicos severamente hidrotratados, biodisel e anti-congelantes (como por exemplo o Etilenoglicol);
→ Boa resistência em meios ácidos e alcalinos e ao Sulfeto de Hidrogénio (Sulfureto de Hidrogênio).
→ Borracha sintética EPDM (Etileno-Propileno-Dieno-Metileno). Um dos tipos de borracha muito utilizada atualmente, pertence ao grupo genérico das “borrachas de etileno-propileno”, que engloba duas variedades de elastômeros: os copolímeros e os terpolímeros.

Fórmula estrutural 12
CURIOSIDADE: Como se pode verificar, a cadeia principal está completamente saturada. Por este motivo, este tipo de borracha apenas é vulcanizável com peróxido.
As borrachas de etileno-propileno-metileno (EPM e EPDM) foram introduzidas em 1962 nos EUA, embora a produção comercial só tenha começado em 1963.
→ Copolímeros são geralmente referidos como borrachas “EPM” (também designados por APK ou EPR), em que as letras “E” e “P” significam respectivamente, Etileno e Propileno, enquanto que a letra “M” significa que a borracha tem uma cadeia saturada do tipo Polimetileno (-(CH2)x-).
→ Terpolímeros, usualmente referidos como borracha de “EPDM”, as letras “E”, “P” e “M” têm o mesmo significado que anteriormente referido, designando a letra “D” o terceiro monómero, um Dieno, que introduz insaturação na cadeia. Os EPDMs são, portanto, EPMs insaturados.
Os dienos mais utilizados são 1,4 hexadieno (1,4 HD), o Diciclopentadieno (DCPD) e o Etilidene Norbornene (ENB), este o mais usado devido à sua fácil incorporação e à sua maior aptidão para a vulcanização com Enxofre, embora seja o mais caro.
Em geral, possuem elevado peso molecular, são amorfas e saturadas e, como dito, pela saturação só podem ser vulcanizadas com peróxidos orgânicos. À temperatura ambiente, o polietileno é um polímero cristalino, mas aquecendo-o, ele passa através de uma fase “elastomérica”. Se interferirmos na cristalização do Polietileno, ou seja, se incorporarmos na cadeia do polímero elementos que impeçam a cristalização, a temperatura de fusão e a fase elastomérica podem ser reduzidas para valores inferiores à temperatura ambiente. Estes materiais amorfos e vulcanizáveis são os EPMs - sendo completamente amorfos e não auto-reforçantes aqueles que possuem entre 45 a 60% de etileno.
Se o conteúdo em etileno for da ordem de 70 a 80%, os polímeros contêm longas sequências de etileno, que são particularmente cristalinas, sendo por isso referidos como graus “sequential” e o seu comportamento em processamento difere muito do apresentado pelos polímeros amorfos.
Uma vez que a vulcanização da borracha de EPM com peróxido, a única possível, apresenta algumas desvantagens, foi desenvolvida a reação do Etileno-Propileno com um Dieno para ser possível a vulcanização com Enxofre e aceleradores convencionais. O produto da polimerização assim obtido é, como já referido, o EPDM, Terpolímero composto por três unidades de monómeros: Etileno, Propileno e Dieno.
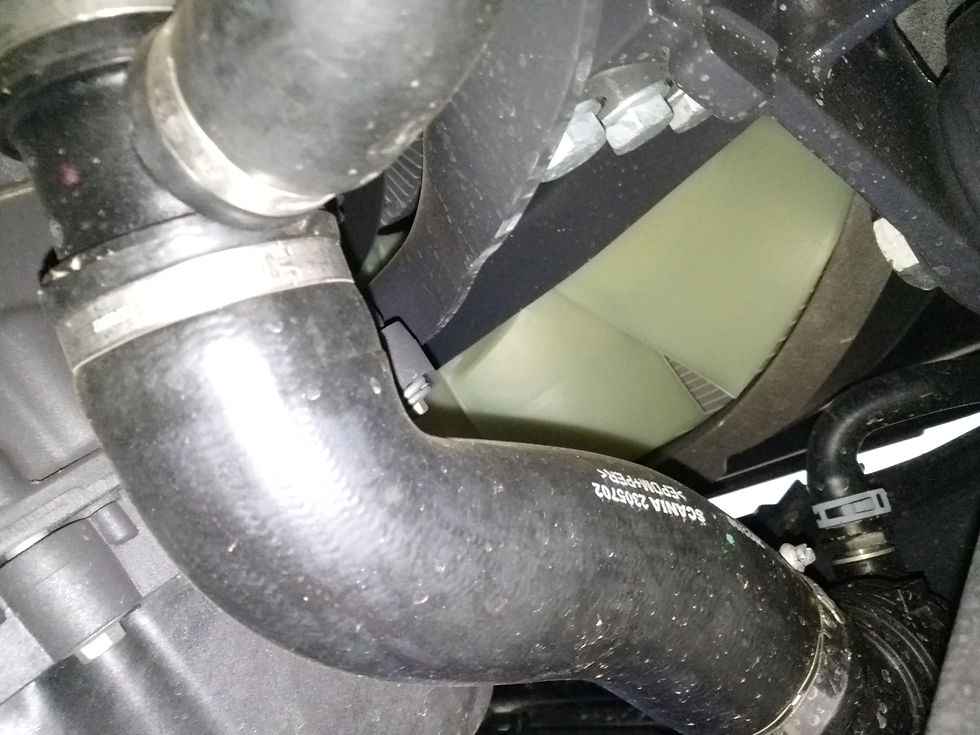
Imagem 3 - Mangueiras do sistema de arrefecimento de um Scania R500 ano 2023
Comumente, as mangueiras do sistema de arrefecimento em motores de combustão interna são feitas de borracha EPDM reforçada com uma malha de PA ou PET. No entanto, apenas o ">EPDM<" acaba sendo destacado nas marcações da peça. No caso da imagem acima, está escrito ">EPDM+PER<", indicando vulcanização com peróxido.
Tendo esta flexibilidade na vulcanização, o EPDM pode usar um processo com Enxofre ou Peróxido, a depender do uso final. EPDM curado com peróxido possui maior resistência a altas temperaturas e baixa deformação por compressão, além de serem resistentes à álcoois (fluidos de freio e de arrefecimento, por exemplo), cetonas, água quente e vapor. Já o EPDM curado com Enxofre possui maior resistência ao rasgo e à tração, além de permitir uma gama mais ampla de enchimentos.
Para além de tudo isso, o EPDM pode ser misturado com resinas termoplásticas para dar origem a um Termoplástico Elastômero, que poder ser vulcanizado ou não. Para saber mais sobre a mistura de plásticos e borrachas e exemplos de uso, CLIQUE AQUI!
→ Borracha sintética ABS (Acronitrila-Butadieno-Estireno): É um copolímero, e a proporção exata de cada componente na composição deste copolímero depende da utilização final do produto para que este se destina. As proporções desta composição podem variar de 15% a 35% de Acrilonitrila (ACN) e 40% a 60% de Estireno, com 5% a 30% de Butadieno. O resultado é uma longa cadeia de Polibutadieno interligada por cadeias curtas de Acrilonitrila com Estireno.
OBSERVAÇÃO: Em muitas aplicações o ABS é encontrado na forma de plástico, porém a Acrilonitrila e o Butadieno - que geram elastômeros - quando adicionados em determinadas proporções podem fazer este copolímero tornar-se borrachoso. Como substituto do ABS podemos citar o seu "primo", o plástico ASA (Acrylonitrile Styrene Acrylate). Para saber mais sobre o ASA, volte ao Capítulo 1 desta série.
Os grupos de nitrilas das cadeias vizinhas, por serem polares, atraem-se uns aos outros ligando as cadeias, fazendo assim com que o ABS seja mais resistente que o poliestireno puro, vulgarmente conhecido por "esferovite". O estireno confere-lhe uma superfície brilhante e impenetrável, e o butadieno, que é uma substância borrachosa, dá-lhe uma flexibilidade que se estende às temperaturas baixas.
O resultado físico deste copolímero é um material termoplástico rígido e leve, com alguma flexibilidade e resistência na absorção de impacto . Esta resina sintética termoplástica pode assumir quaisquer formas e cores, por moldagem térmica a altas temperaturas e adição de pigmentos.
As resinas ABS podem ser encontradas em tipos adequados para moldagens por injeção, extrusão, por sopro, expansível e para conformações a quente. Alguns tipos de ABS são misturados com outros tipos de resinas tendo a finalidade de atingir propriedades específicas, como por exemplo alterar a rigidez do PVC para sua utilização em tubos, chapas e peças moldadas.
CURIOSIDADE: A produção de 1 kg de ABS requer o equivalente a cerca de 2 kg de petróleo como matéria-prima. Ainda na consideração de custos de produção deve ser levado em consideração a energia gasta em seu processamento, entre outros custos fixos, o que ainda assim configura o copolímero ABS em um plástico barato e com bom relação custo-beneficio quando considerada sua durabilidade e resistência mecânica.
Os polímeros de ABS são resistentes a alcalinos, ácidos aquosos, ácidos hidroclorídrico e fosfórico-concentrados, álcoois e óleos animais, vegetais e minerais, mas são inchados por ácido acético glacial (que é o componente ácido do vinagre), tetracloreto de carbono e hidrocarbonetos aromáticos. São atacados também pelos ácidos sulfúrico e nítrico-concentrados, e são ainda solúveis em ésteres, cetonas e organoclorado de etileno. As características de envelhecimento dos polímeros são provocadas pela quantidade de polibutadieno e, por isto, é normal incluírem-se antioxidantes na sua composição.
O ABS é inflamável quando exposto a altas temperaturas. As características de impacto das resinas ABS são excepcionais à temperatura ambiente, e em determinados tipos destas resinas chegam a resistir à temperaturas baixas de até -40 °C.
→ Borracha sintética FPM: A designação FPM ou FKM (Normas DIN/ISO 1629 ou ASTM D 1418, respectivamente), são as que representam aproximadamente 80% dos fluoroelastómeros, sendo que todos eles (FPM e FKM) contêm fluoreto de vinilideno (VF2) como um monómero.
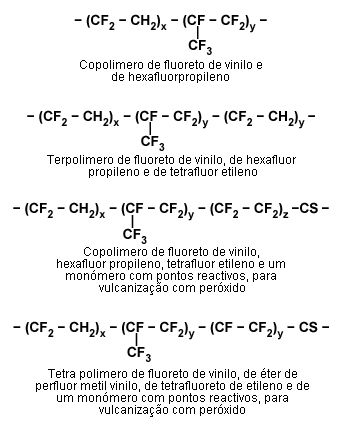
Fórmulas estruturais 13
Os fluoroelastômeros são borrachas altamente especializadas e o seu aparecimento foi de grande importância para a resolução de problemas existentes nas indústrias automotiva, aero-espacial, química e petrolifera. Devemos referir também os elastômeros perfluorados (FFPM e FFKM), terpolímeros que são totalmente fluorados e utilizados em ambientes de extrema agressividade química, já que apresentam a melhor resistência química de todos e suportam temperaturas da ordem de 325 °C, assim como as borrachas de tetrafluoretileno e propileno (FEPM ou TFE/P), copolímeros que também possuem VF2 como monómero.
Os elastómeros fluorados são todos fruto da descoberta da inércia do politetrafluoretileno (PTFE) feita por Plunkett em 1938, descoberta essa que posteriormente originou a marca comercial Teflon, da DuPont, tendo os primeiros produtos surgidos a partir de 1950.
Inicialmente foi a descoberta de um copolímero de fluoreto de vinilideno (VF2) e hexafluorpropeno (HFP) e, pouco depois, a de um outro termicamente mais estável e mais resistente aos solventes, o terpolímero VF2/HFP/TFE, que possui um conteúdo elevado de flúor comparado com os copolímeros. A estes produtos foi dado o nome comercial "VITON A" (copolímero lançado no mercado em 1958) e "VITON B" (terpolímero), que tiveram como concorrente o "FLUOREL" (nome comercial da 3M Company) e mais tarde o DAI-EL (da Daikin Kogyo Company, do Japão) e o "TECNOFLON" (Montecatini).
Foi igualmente marcante a descoberta do primeiro perfluorcarboneto elastômero, um copolímero de TFE/ter de perfluormetilvinil (PMVE), o mais estável de todos os elastómeros conhecidos e que, com a adição de PMVE ganhou uma flexibilidade a baixa temperatura muito superior à dos copolímeros e dos terpolímeros.
A maioria dos elastómeros de VF2/HFP e VF2/HFP/TFE (tetrafluoretileno) são normalmente preparados por polimerização radical em emulsão usando compostos “perxi” tais como persulfato de amónio como iniciador, ocasionalmente em sistemas “redox” com ou sem agentes de transferência de cadeia tais como tetracloreto de carbono, ésteres alcalinos ou sais halogenados. A normal polimerização contínua é seguida por centrifugação ou coagulação e isolamento do polímero seco.
CURIOSIDADE: A maior parte das vulcanizações de FPM é efetuada em duas etapas: uma vulcanização sobre pressão em prensa (compressão, transferência ou injeção) ou em autoclave até que o produto tenha uma estabilidade suficiente e uma pós-vulcanização em estufa sem pressão com circulação de ar quente para complementar a reação de reticulação. Durante a vulcanização formam-se pontos de reticulação enquanto que o polímero liberta fluoreto de hidrogénio, HF, o qual reage com o Óxido de Magnésio formando Fluoreto de Magnésio (MgF) e água. Para que a reticulação fique totalmente completa é necessário que a água formada seja removida o que só é possível na totalidade durante a pós-vulcanização em estufa.
Em geral, a maioria dos compostos necessita, como referido, de um ciclo de vulcanização com duas etapas para atingir o melhor balanço das propriedades do vulcanizado. A vulcanização pode ser à temperaturas na faixa dos 200 ~ 204 °C durante poucos minutos ou, sendo efetuada em vapor durante 2 a 3 horas. Para artigos bastante espessos é normal usar-se uma vulcanização em que a temperatura sobe gradualmente, podendo uma vulcanização gradual típica se iniciar a uma temperatura de 80 °C e esta ir subindo em etapas de 30 °C. Deve seguir-se à vulcanização uma pós-vulcanização em estufa durante, por exemplo, 15 horas a 230 °C (pode ser de 24 horas a uma temperatura um pouco mais baixa), para otimizar as propriedades de tensão de rotura e de resistência à compressão, embora, por vezes 10 horas seja já uma duração suficiente, podendo, todavia, serem utilizadas temperaturas mais elevadas para alguns tipos de borrachas fluoradas. A temperatura da estufa deve ser tão alta quanto a temperatura prevista para a utilização do componente de borracha.
As borrachas fluoradas são excepcionalmente estáveis a alta temperatura, são excelentes em serviço quando expostas continuamente a temperaturas de 240 ~ 260 °C, apresentando uma excelente resistência à compressão a temperaturas elevadas e boa flexibilidade a baixa temperatura. Suportam, por períodos de pequena duração , temperaturas da ordem dos 300 ~ 310 °C.
Apresentam resistência química a hidrocarbonetos alifáticos, aromáticos e clorados, óleos de silicone, óleos e massas minerais, combustíveis de prova de Referência A,B,C e D apresentando, após imersão de 70 h a 150 °C, aumentos de volume de 0 a 1 %, de 2 a 4 %, de 3 a 8 % e de 8 a 12 %, respectivamente. O aumento de volume nos óleos de Referência IRM 901, IRM 902 e IRM 903, nas mesmas condições mencionadas anteriormente, de 0 a 1 %, de 1 a 2 % e de 3 a 5 %, respectivamente.
Não são resistentes a solventes polares como acetona, metiletilcetona e acetato de etilo, fluídos de freio à base de glicol, ácido fórmico, ácido acético e ácido clorosulfônico.
Os compostos de FPM vulcanizados com peróxidos apresentam melhor resistência ao vapor do que os vulcanizados com difenol ou diamina. A resistência ao vapor aumenta com o conteúdo em flúor.
As borrachas FPM estão situadas no primeiro patamar das borrachas sintéticas devido, para além das propriedades já referidas e dos elevados valores mecânicos que apresentam, excelente resistência ao envelhecimento e ao ozônio.
A borracha fluorada tem um peso específico elevado (1,80 a 1,85) e é uma das borrachas mais caras existentes no mercado, fatos que adicionados à elasticidade a baixas temperaturas nem sempre ser necessária, diminuem a sua utilização.
→ Borracha de Isopreno (IR): A borracha de isopreno ou poliisopreno é uma espécie de material “natural sintético”, ou seja, é um cis-1,4-poliisopreno obtido sinteticamente. A característica técnica do produto sintético depende da porcentagem de 1,4 cis, isto é, quanto mais cis contém, mais se parece com a borracha natural (NR).
Como a estrutura química é quase similar à da borracha natural, o campo de aplicação da IR é semelhante ao da NR, embora a borracha IR seja bastante mais pura. A maior parte da borracha de isopreno é formulada juntamente com borracha natural (NR) ou borracha de estireno butadieno (SBR), necessitando todavia de uma quantidade de aceleradores superior ao da borracha natural.
As primeiras tentativas na pesquisa de borrachas sintéticas, tinham por finalidade obter uma borracha semelhante à borracha natural, usando o isopreno como material de partida. Em 1954, Goodrich foi bem sucedido na síntese do cis-1,4-poliisopreno, a então chamada “borracha natural-sintética” usando os agentes catalíticos de Ziegler-Natta (Carlos Ziegler e Júlio Natta), tetracloreto de Titânio e trialquil-Alumínio. Pouco depois, Firestone descobriu o caminho para a síntese de IR usando Lítio finamente disperso e alquil-Lítio como agentes catalíticos, o que já tinha sido proposto por C.D. Harries em 1917. A produção em grande escala de borracha de isopreno (IR) utilizando Lítio foi inicializada em 1960 pela Shell, mas somente foi comercializada em 1962 pela Goodyear.
→ Borracha de IIR (copolímero de isobutileno e isopreno): É conhecida como borracha butílica e foi introduzida no mercado em 1942. É considerada como pertencente à categoria das borrachas para aplicações especiais (SPR). A borracha butílica é um composto polimerizado em solução de isobutileno com uma pequena percentagem de isopreno catalizada por AlCl3 dissolvido em cloreto de metilo. Na Fórmula abaixo é apresentada a estrutura da borracha butilica:

Fórmula Estrutural 12
As borrachas butílicas de diferentes fabricantes distinguem-se do ponto de vista químico pela viscosidade, estabilização e conteúdo de isopreno que varia de 0,6 a 3%, normalmente na ordem de 2%, sabendo-se que um conteúdo elevado de isopreno aumenta a velocidade de vulcanização, porém diminui a resistência ao ozônio e ao envelhecimento. Na produção da borracha IIR, o isopreno pode adicionar-se à cadeia principal de três formas diferentes: 1,2; 3,4 ou 1,4 adição.
O relativo baixo grau de insaturação apresentado pela borracha IIR, comparativamente com o das borrachas de NR, SBR, BR, CR e NBR é o responsável pela grande resistência ao oxigénio, ozonio e calor.
A borracha butílica sofreu a partir de 1986 uma forte concorrência da borracha EPDM devido a algumas vantagens oferecidas por esta última.
Vulcanização do Butil
A borracha IIR pode ser vulcanizada por três métodos básicos:
→ vulcanização com enxofre e aceleradores; → vulcanização com quinona dioxima; → vulcanização com resina de fenol formaldeído.
Também podem ser utilizados outros sistemas de vulcanização para a borracha butil. É necessário, as vezes, o uso de um acelerador secundário no sistema de vulcanização. Nesta situação é frequente usarem como dadores de enxofre polímeros de dissulfureto de alquil fenol (por exemplo, um da série comercial Vultac) com porcentagem em massa de enxofre variável entre 18% e 30% e pontos de amolecimento variáveis entre 55°C e 120°C.
Propriedades Características do IIR
Os vulcanizados de borracha butílica apresentam como propriedades características:
→ Elevado amortecimento (valores elevados de tang δ); → Muito baixa permeabilidade ao gás e ao ar; → Boa rigidez dielétrica; → Boa resistência ao ozonio e intempéries; → Muito boa resistência ao vapor e ao calor seco; → Boa resistência a óleos e gorduras de origem animal e vegetal; → Boa flexibilidade a baixas temperaturas; → Elasticidade limitada à temperatura normal; → Boa resistência à compressão; → Boas propriedades de vedação; → Impermeável ao dimetilformamide (DMF), que é um solvente eletrolítico comum.
Considerando a química do copolímero IIR, sua resistência aos óleos é baixa e não comparável à apresentada pela borracha natural (NR) e pela borracha de polibutadieno (BR), já que, a borracha butílica, tal como a borracha de acrilonitrilo butadieno (NBR), não contém hetero-átomos tais como N ou O, que normalmente reduzem a compatibidade com os óleos minerais. Com isto, podemos concluir que a borracha butílica não resiste a óleos minerais, a hidrocarbonetos alifáticos, aromáticos e clorados, muito menos a combustíveis como a benzina e o diesel.
CURIOSIDADE: Existem duas classificações gerais e genéricas para compostos de borracha:
-> Borrachas para aplicações especiais (SPR): São exemplos o FPM e FKM, bem como a borracha de IIR e a borracha EPDM;
-> Borrachas para aplicações gerais (GPR): São exemplos a borracha natural (NR), a borracha de butadieno estireno (SBR) e a borracha de polibutadieno (BR).

Este foi mais um capítulo da série sobre ciência e tecnologia dos materiais (CTM).
No próximo artigo será explicado o que são os termoplásticos elastômeros, um material que pode ser substituir a borracha em algumas aplicações.
Para mandar dúvidas, sugestões ou críticas construtivas ao blog, mande um e-mail para hardwarecentrallr@gmail.com.
FONTES e CRÉDITOS:
Texto: Leonardo Ritter
Imagens e gráficos: Google Imagens, Khan Academy, ctborracha; Rubberpedia; Brasil Escola.
Fontes: Rubberpedia (Manuel Morato Gomes); Brasil Escola (Jennifer Fogaça); SABÓ; ANIP (Associação Nacional da Indústria de Pneumáticos); Khan Academy; ctborracha; Dutra Borrachas; Afinko Polímeros; AkroPlastic; Wikipedia (somente artigos com fontes verificadas!).
Última atualização: 31 de Janeiro de 2025.
Comments