Excepcional - Propriedades Mecânicas dos Materiais (PARTE 3)
- Drano Rauteon
- 21 de set. de 2023
- 21 min de leitura
Atualizado: 24 de nov. de 2024
Para aquecer o cérebro, que tal dissertarmos sobre o resistência de um material quando submetido a impactos?
Resistência ao impacto
Estendendo o tópico "Tensão de Ruptura?" do artigo anterior, o ensaio de impacto permite determinar a energia absorvida na deformação e ruptura do corpo de prova. Quanto menor for esta energia absorvida, mais frágil será o comportamento do material àquela solicitação dinâmica.
De acordo com o Sistema Internacional (SI), a resistência ao impacto é expressa em termos de energia absorvida por unidade de espessura (J/mm ou J/m) ou unidade de área (J/mm³). Também pode ser dada em kgf.mm.
Outra medida importante relacionada ao ensaio de impacto com amostra entalhada, e mais significativo quando realizado em um intervalo amplo de temperaturas, é a temperatura na qual ocorrer a transição dúctil-frágil em materiais que apresentam esse fenômeno, além de ser empregado na verificação do efeito da temperatura na tenacidade em diversos tipos de materiais.
A curva de transição dúctil-frágil é influenciada por diversos fatores, entre eles a estrutura cristalina, composição química, tratamentos térmicos e conformação mecânica dos materiais.
A maioria dos polímeros e cerâmicas também apresentam transição dúctil-frágil, entretanto, para as cerâmicas essa transição é observada apenas em temperaturas elevadas, ordinariamente acima de 1000 °C.
Para polímeros, além da temperatura, a velocidade de ensaio, a umidade relativa do ar e as tensões residuais do processo de moldagem também devem ser controladas para a obtenção de resultados adequados e condizentes com a aplicação do componente.

Imagem 1 - Blocos de EPP são absorvedores de impactos na dianteira e traseira de veículos modernos
O uso do Polipropileno Expandido é amplo na indústria automobilísca dada a sua capacidade de absorção de impactos sucessivos sem se deformar ou rasgar, ou seja, ele é bastante elástico, até mais do que o Poliestireno Expandido (EPS).
CURIOSIDADE: O ensaio de impacto consiste em submeter um corpo de prova (metálico, cerâmico, polimérico ou borrachoso), geralmente entalhado e com dimensões padronizadas, a uma flexão provocada pelo impacto de um martelo pendular. Os resultados são apresentados relacionando a energia absorvida durante o impacto em relação à temperatura da amostra.

Imagem 2 - Os dois métodos para ensaio de impacto
Na imagem acima o corpo a ser provado está em vermelho (perceba o entalhe na amostra) e o cone amarelo indica a posição de ataque do martelo pendular. "Charpy" e "Izod" são os nomes dados aos métodos de aferição.
No gráfico abaixo temos o valor aproximado de resistência ao impacto para alguns materiais:

Gráfico 1 - Comparação de resistência entre polímeros
OBSERVAÇÃO: "UTEC" é o nome comercial da Braskem para seu produto de PE-UHMW.
No tópico anterior (PARTE 2 deste texto) dissertamos um pouco sobre as lentes de faróis e lanternas. Pois bem, note que o Policarbonato consegue mais de 600 J/m, enquanto o PMMA fica próximo de 0 J/m. Diferente do EPP, o Polipropileno puro tem uma resistência baixa, inferior aos 100 J/m. Já o PE-UHMW consegue chegar próximo das ligas de aço, ficando em torno dos 1 mil J/m. O ABS pode ser uma incógnita, já que sua resistência ao impacto também depende da porcentagem de cada um de seus componentes (Acrilonitrila, Butadieno e Estireno).
Vidros temperados tendem a ter uma resistência um pouco maior que os comuns, mas ainda assim valores tão baixos quanto o PMMA. Já as cerâmicas, nem precisa dizer...
Resistência à compressão
O esforço de compressão é a resultante das pressões aplicadas em um sólido deformável ou meio contínuo, caracterizada porque tende a uma redução de volume ou um encurtamento, empenamento (flexão ou torção) em determinada direção.
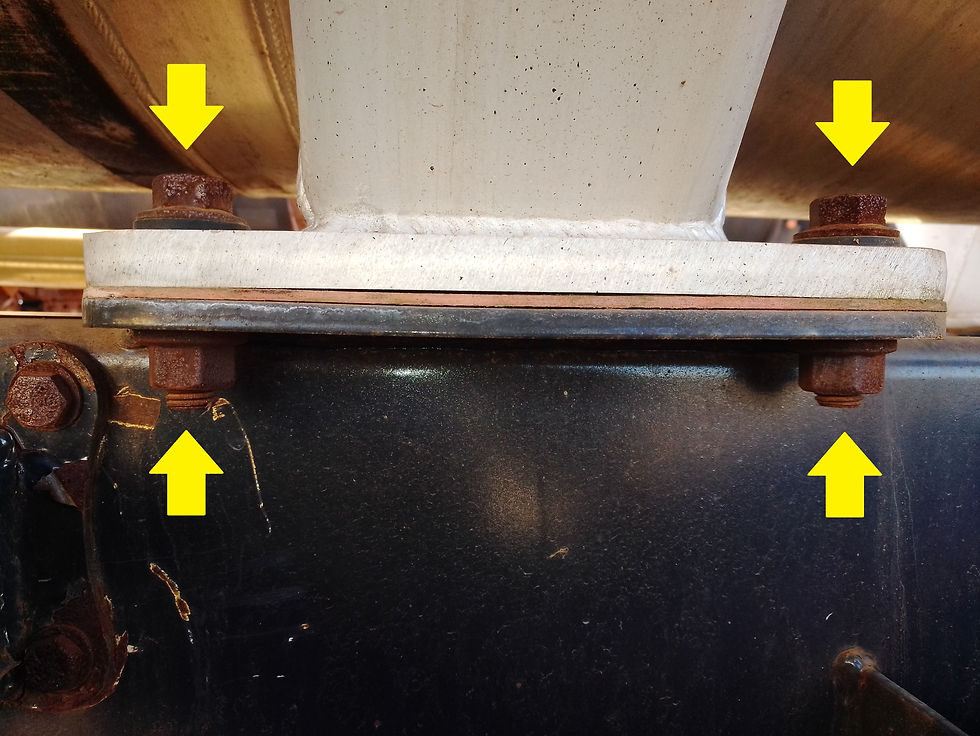
Imagem 3 - Sapatas de fixação do berço de um tanque na longarina de um chassi num semi-reboque da Triel-HT
Note na figura acima que os parafusos e polcas estão tracionados (apertados), fazendo a compressão entre a chapa de AlMgSi, a chapa de Aço-liga, as arruelas plásticas (abaixo da cabeça de cada parafuso) e a junta plástica (folha de papelão hidráulico de cor alaranjada) que faz a interface entre as duas estruturas. Perceba o abaulamento na região central, não comprimida, com pequenas frestas.
CURIOSIDADE: Você já deve ter notado que o macaco que vem junto do pneu reserva no porta-malas do seu veículo é do tipo 'sanfona' ou 'joelho' e com elevação puramente manual. Macacos do tipo 'garrafa' ou 'jacaré', com elevação por pistão hidráulico são mais caros e acabam reservados pra quem trabalha com mecânica.

Imagem 4 - Os mais simples e baratos são os do tipo 'joelho' e 'sanfona'
Mas e quando o fabricante do automóvel resolve unir um formato mais robusto com um material mais barato e o acionamento mais simples?
Foi numa sacada dessa que os russos da Lada criaram um macaco do tipo 'garrafa' em PA6-GF30 e com acionamento na base da força do braço:

Imagem 5 - O macaco do Lada Vesta têm capacidade nominal para 550 kG (e por incrível que pareça aguenta até um pouco mais do que isso) e é feito em PA6-GF30
O formato geométrico diz muito sobre este equipamento. Faça o experimento em casa: tente apoiar alguma massa sobre duas tiras de papelão e depois sobre um tubo de mesmo material pra ver qual aguenta mais. A geometria cilíndrica permitiu o uso de plástico e lã de vidro em substituição ao tradicional metal, simplificando e barateando o produto. Este é um belo exemplo de como a forma geométrica traz a possibilidade de uso de outros materiais para a confecção de um sistema robusto.
E geral, quando se submete um material a um conjunto de forças se produz tanto cisalhamento, flexão e ou torção, todos estes esforços conduzem a aparição de tensões tanto de tração como de compressão.
Citando mais uma vez os sistemas de suspensão HaulMaax e UltiMaax da Hendrickson, suas molas de carga progressiva e molas de cisalhamento, feitas de borracha precisam suportar constantes oscilações de compressão quando o veículo está carregado e passando por solo irregular, ou seja, o coeficiente de Poisson é próximo de 0,7 e o módulo de Young é mais baixo do que o de uma mola helicoidal feita de liga metálica.
Vídeo 1 - A unidade de medida da resistência à compressão é o Pascal (Pa)
Agora imagine um pneu de caminhão. Em geral eles precisam ser calibrados com uma pressão em torno de 120 PSI (Libras por polegada quadrada), o que dá em torno de 827 kPa.

Imagem 6 - De cima para baixo: Michelin, Firestone e Goodyear
Um pneu não só precisa aguentar os mais de 800 kPa de ar comprimido em seu interior, mas também a massa localizada do veículo sobre ele (o eixo dianteiro de um caminhão-trator, por exemplo, distribui entre 2 e 3 toneladas por roda), que o comprime contra o solo.
Talvez o melhor exemplo de compressão quando se trata de mecânica automotiva são as juntas de vedação para fluídos e gases. São componentes de grande elasticidade que ficam comprimidos entre duas peças com pouca elasticidade. A compressão através do tracionamento de parafusos ou de grampos vedam o sistema e impedem o vazamento dos mais diversos produtos.

Imagem 7 - Uma válvula de fundo montada com dois anéis vedadores, que neste caso podem ser feitos de Fluoelastômero ou PoliTetraFluorEtileno
Como o módulo de Young é baixo, é necessário um aperto muito grande para cisalhar o vedador, porém, existe o risco, já que são vários fixadores e a área de contato é pequena.
Nos motores de combustão interna as juntas estão presentes em todos os lugares. Neste caso há o adendo da temperatura, já que podem operar acima dos 100 °C, então um excesso de aperto pode romper o elemento elástico na fase aquecida, ou então provocar um empenamento, uma deformação dos componentes.
OBSERVAÇÃO: No caso da Imagem 3, o abaulamento entre fixadores é tolerável, porém, para vedar gases ou líquidos seria inadmissível!
Ficou claro que os materiais, quando experimentam um esforço de compressão são limitados pelas mesmas variáveis (módulo de elasticidade, cisalhamento e coeficinete de Poisson) levadas em conta na força de tração.
Resistência ao atrito
A fricção entre peças móveis deve ser levada em conta num sistema mecânico, afinal, isso gera desgaste e manutenção, coisas que devem ser suavizadas ao máximo para se ter uma boa durabilidade.
Dentre os metais, ligas de Bronze, Latão e Alumínio são demasiadamente aplicadas em componentes de desgaste. No vídeo abaixo, a barra de tucho de uma serra tico-tico desliza sobre bronzinas apoiadas em mancais de PA66-GF35 (a própria carcaça do equipamento):
Vídeo 2 - Note que o tubo de Aço-liga desliza por dentro das buchas de Bronze. Obviamente carecia de lubrificação com graxa, e o fiz posteriormente
Já com os polímeros, o trio Poliamida (PA, mais conhecido como Nylon, Tecalon ou Tecnil), Polietileno de Ultra Alto Peso Molecular (PE-UHMW) e PoliTetraFluorEtileno (PTFE, mais conhecido como Teflon) são amplamente usados pela indústria, sendo o primeiro o de menor desempenho, no entanto, o mais barato.

Gráfico 2 - Coeficiente de fricção para alguns materiais poliméricos
OBSERVAÇÃO: Os valores do gráfico são comparações gerais, pois o atrtito depende de uma série de fatores internos e externos ao material.
Veja que a adição de Carbono (variação alotrópica Grafite) gera uma grande mudança - pra melhor - no coeficiente de atrito. Talvez a ideia de usar pinos de Carbono para fazer a conexão elétrica com o rotor em alguns tipos de motores não tenha sido a toa!

Imagem 8 - Um motor elétrico CA 220 Volts com escovas de "carvão"
Note que o anel coletor, isto é, a pista em que os dois pinos estão em contato é feita com uma liga de Cobre, que além de conduzir energia também forma a combinação perfeita para se conseguir um baixo atrito, obtendo-se assim uma ótima durabilidade, além de fácil manutenção, já que as escovas são apenas encaixadas.
Um fator interessante também é que quem define o perfeito contato elétrico e o nível de fricção das escovas no anel coletor são as molas helicoidais que pressionam-as contra a pista. Quanto maior for a força de compressão aplicada sobre dois corpos em atrito, maior tende a ser a resistência ao movimento.
Se você analisar a estrutura da quinta-roda Jost - vista na PARTE 1 deste texto - do ponto de vista químico, notará uma porcentagem significativa de Carbono, afinal o prato é uma liga de Ferro fundido.
CURIOSIDADE: Ainda assim, para se eliminar a graxa entre o prato da quinta-roda e a mesa do trailer, muitas empresas optam por uma capa de plástico como 'placa de desgaste'. Quando montada na mesa, costuma ser PE-UHMW, já quando montada na quinta-roda costuma ser feita de PA. No final, o atrito acaba fazendo com que fragmentos de plástico sejam gerados, apesar de serem bastante duráveis...
Os automóveis atuais (virada do século pra cá) costumam ter limitadores de porta com hastes de PA. Para ter uma ideia do funcionamento de tais peças, observe o diagrama:

Diagrama 1 - Os quadros azuis representam os estágios de abertura da porta. A quantidade de estágios depende do projeto, mas no geral vai de um a três
Note que, assim como as escovas dos motores, os roletes de metal são pressionadas contra a 'pista' por uma ou duas molas helicoidais. Estes roletes podem ser feitos de Aço-liga. Em projetos mais antigos até mesmo a haste era feita de liga de aço.
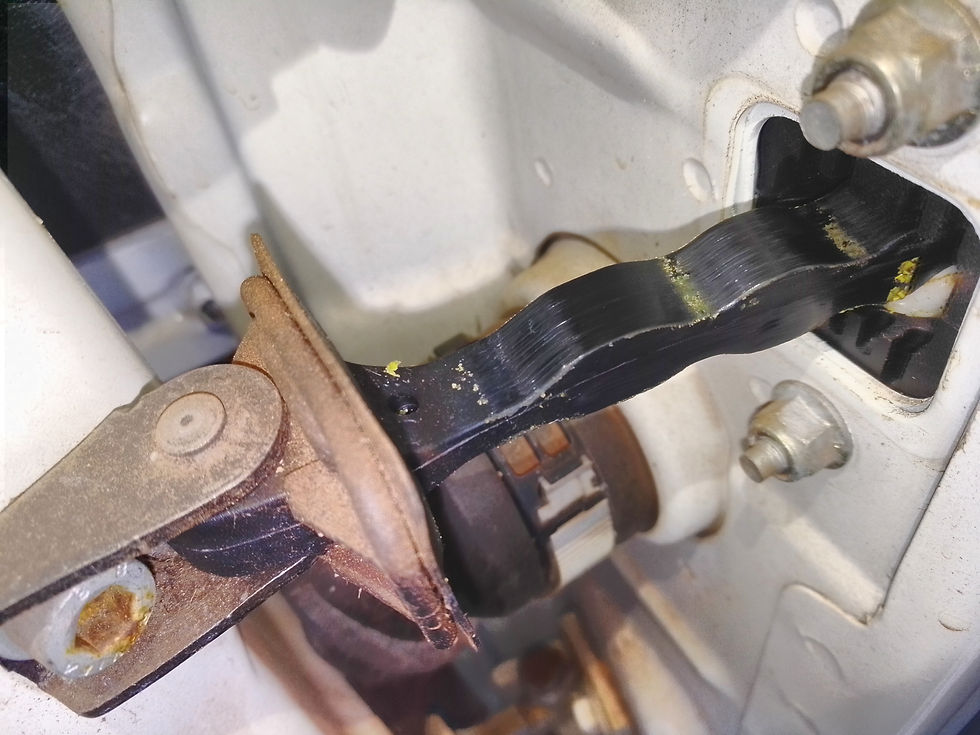
Imagem 9 - Note o desgaste na haste de Poliamida causada pelo deslizamento dos roletes. Este limitador é de um Palio Attractive
Agora observe este outro limitador:
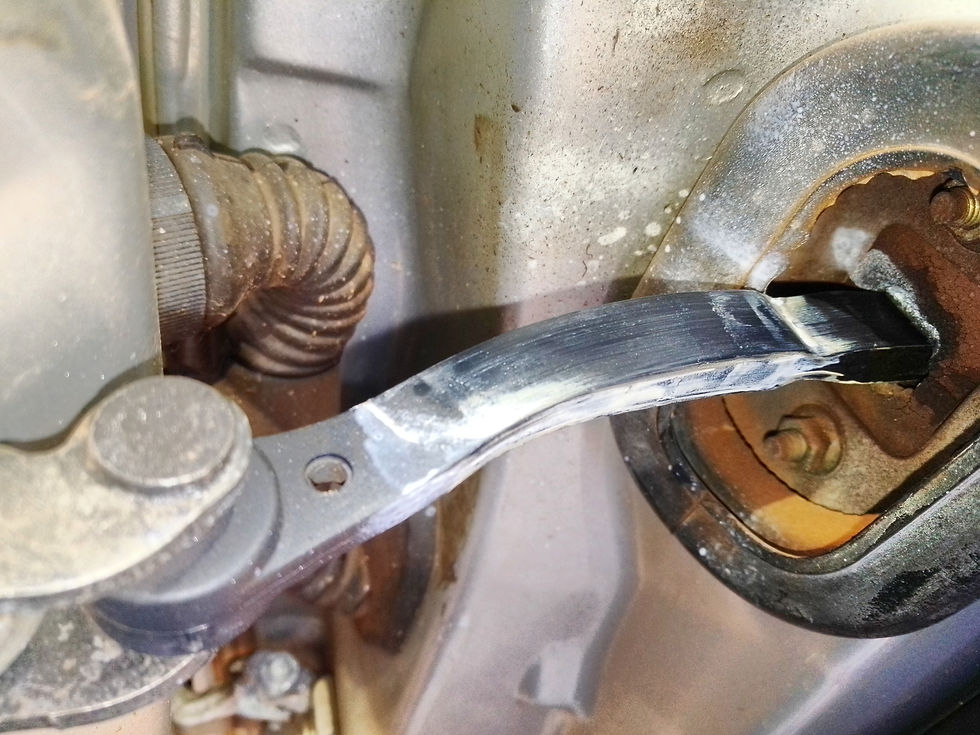
Imagem 10 - Note que mesmo com graxa lubrificante há sinais de desgaste provocados por fricção. Este é de um Ford Focus MK1
Um bom exemplo de uso do PA como elemento de desgaste é neste modelo de tampa para tanques e silos rodoviários:

Imagem 11 - Perceba que cada manípulo de liga de Alumínio atrita com um componente removível (parafusado) feito de plástico. Qual precisará de substituição primeiro?
A Poliamida também é amplamente utilizada em pivôs de suspensão de veículos leves e pesados, no entanto, é comum a aplicação de graxa para retardar o desgaste, bem como a vedação com coifa para impedir o contato com a sujeira, que costuma ser abrasiva...
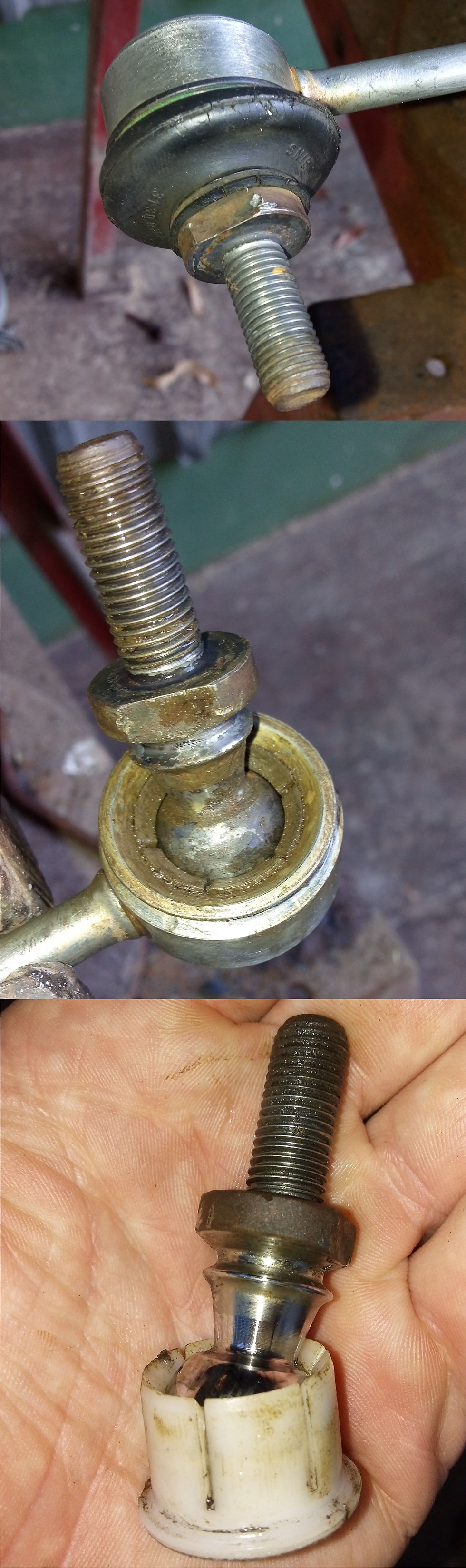
Imagem 12 - Um pivô é uma articulação baseada numa haste com ponta esférica, que por sua vez é encaixada em uma bucha
A esfera de aço da articulação precisa ser bastante lisa, polida, pois quanto menos aspereza, rugosidade, menos fricção. Quando desgastadas, costumam ficar bastante 'molengas', já que o uso contínuo criou uma folga na bucha.
A aplicação de plástico também pode ser feita em rolamentos:
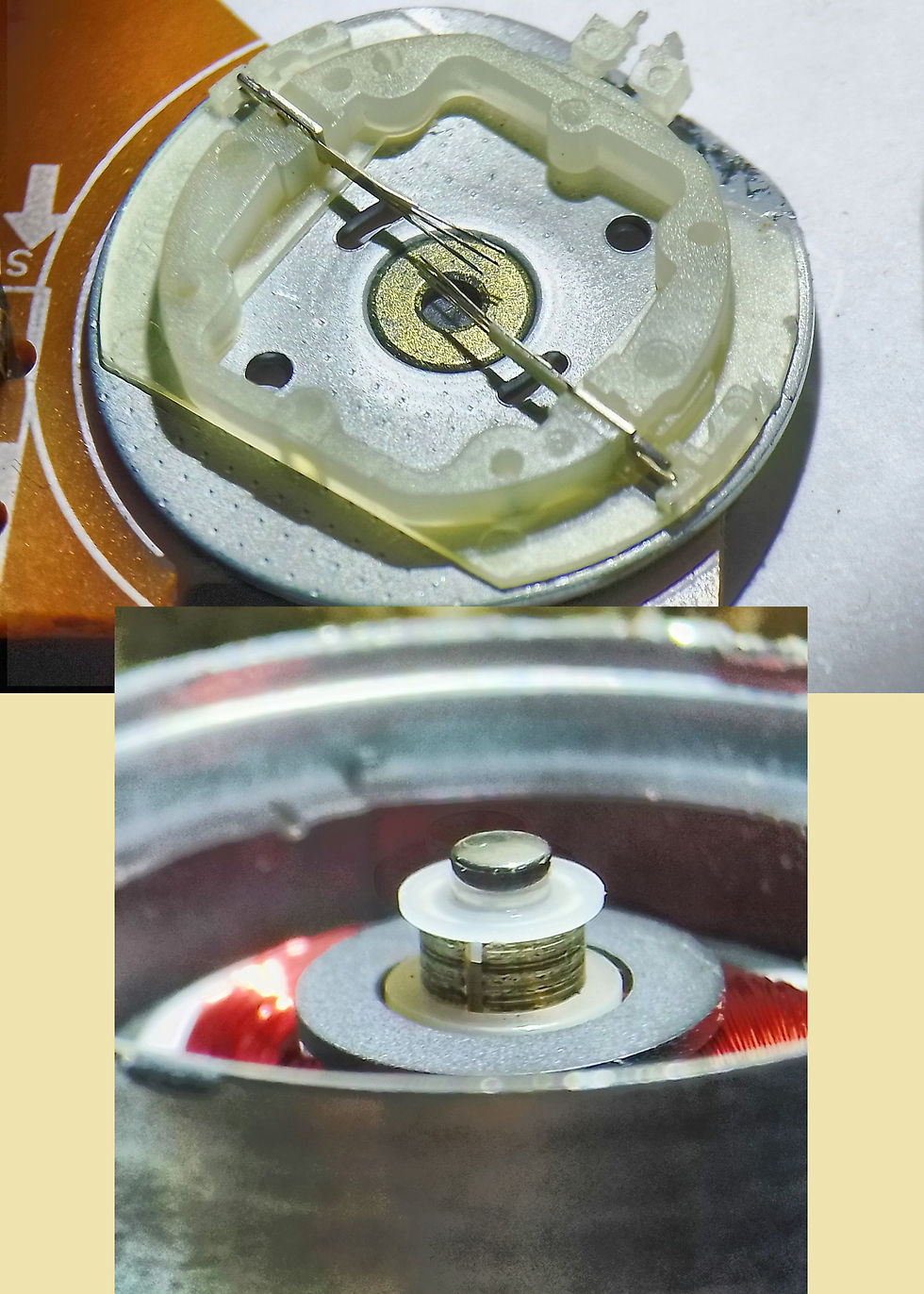
Imagem 13 - Rolamento de um motor DC5.9 Volts retirado de um drive de mídias ópticas
Na imagem acima temos a combinação da Poliamida com uma liga de Cobre, que até então não sabemos se é Bronze ou Latão.
O coeficiente de atrito não é uma propriedade intrínseca do material, bem pelo contrário, depende não só das próprias características da superfície mas também das especificações da face do outro elemento que estará sendo friccionado nele, além da já dita força de compressão entre os corpos. O atrito depende também das condições ambientais (quente ou frio, que gera dilatação e contração), da adição de lubrificantes sólidos, líquidos ou pastosos...
CURIOSIDADE: Os sistemas de transmissão de movimento utilizando polias e roldanas com correias é um dos que menos tem atrito quando comparados com sistemas de transmissão com engrenagens ou correntes. Em tais projetos a PA, o PE-UHMW e o PTFE também são aplicados para maximizar a redução de atrito.
Para saber mais detalhes sobre a força de atrito utilizando como exemplo prático sistemas de transmissão de movimento e rolamentos, CLIQUE AQUI!
Mas e quando o atrito é essencial?
Já parou pra pensar que em alguns sistemas o atrito é fundamental?
O freio do seu carro, por exemplo, é basicamente um conversor de energia cinética em energia térmica através da fricção. Para isso se utiliza dois elementos mecânicos bi-apoiados sofrendo compressão:
-> Um rotor, que se movimenta junto com a roda;
-> Um estator, imóvel, fixo no estrutura da suspensão;
Observe este tambor de caminhão:

Imagem 14 - No Brasil, o sistema de freio a tambor é demasiadamente comum na frota nacional de implementos rodoviários
A interação entre os dois quando se pisa no freio permite ajustar a fricção de acordo com a necessidade do momento. Num sistema sem ABS, uma freada 'violenta', brusca, resulta em travamento das rodas e perda de controle do veículo. Em suma, a força de compressão entre rotor e estator é dinâmica, isto é, se altera dentro de uma faixa de valores conforme a necessidade do condutor.
Os materiais aplicados no rotor comumente são ligas de Ferro fundido, seja um sistema de tambor ou um sistema de disco. Já o estator é geralmente um compósito abrasivo feito de materiais orgânicos e inorgânicos em forma de pó e fibras, tudo unido por um aglutinante.
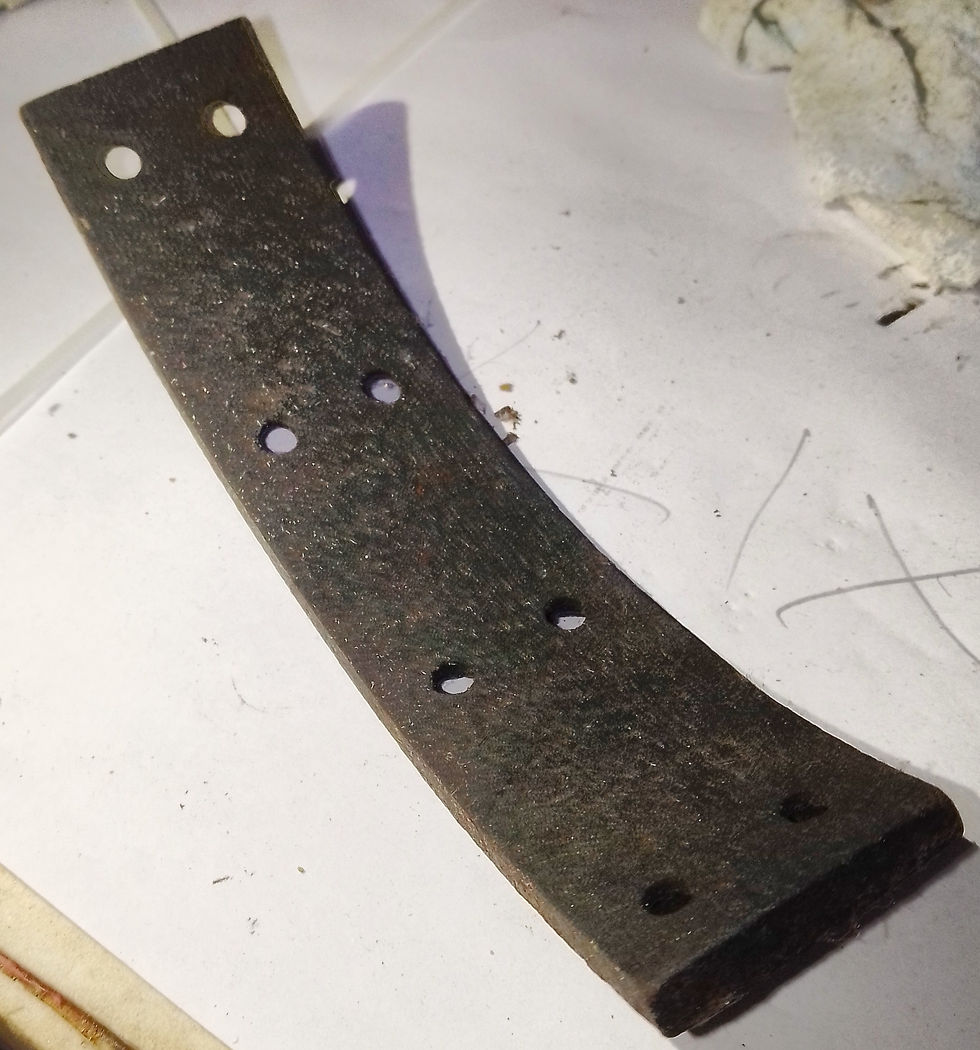
Imagem 15 - Perceba que a superfície é bastante áspera, além de ser difícil distinguir o material
CURIOSIDADE: O material abrasivo, também conhecido como "lona de freio", apesar de ter alguma elasticidade sofre de fratura frágil facilmente, e por isso necessita ser fixado com rebintes - note os vários furos - numa peça metálica de apoio, que por sua vez é montada em um suporte na ponta do eixo. O conjunto apoio+lona forma o popularmente conhecido "patins de freio" ou "sapata de freio".
Compósitos para freio, apesar dae uma certa fragilidade, possuem um grau de maciez fundamental para não serem apenas "esfoladores" de rotores e proporcionarem uma pressão adequada contra o disco ou tambor. Generalizando o assunto, é comum que bicicletas mais simples possuam um sistema de freio com pastilhas de borracha atritando diretamente na borda do aro da roda. A compressão feita na borracha funciona de forma análoga ao auto-travamento de fixadores com arruelas de plástico ou borracha descritos na PARTE 1 deste texto.
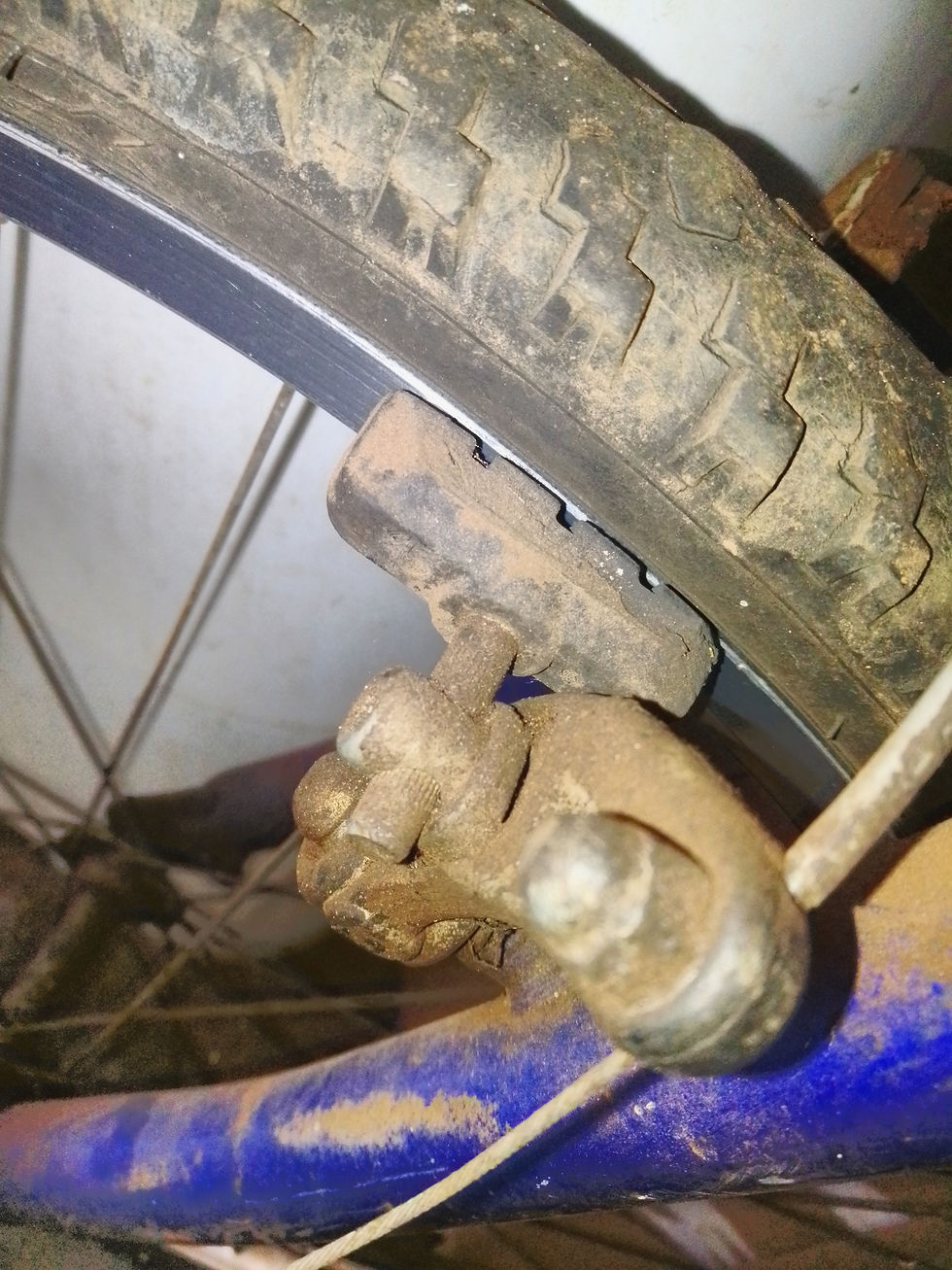
Imagem 16 - Pastilha de freio composta por elastômero
Num sistema de freio automotivo, os estatores (as lonas e pastilhas) são os que se desgastam mais rápido e precisam de substituição frequente. A vantagem é que custam um valor baixo se comparado aos rotores (discos e tambores). Tambores costumam durar muito mais que os discos se fôr levar ao 'pé da letra', no entanto, tendem a ter menos eficiência e maior aquecimento nas frenagens.
Indo ainda mais longe no assunto atrito, fazendo um rotor abrasivo em formato de disco e encostando sua borda sob alta rotação num estator metálico fixo, podemos corta-lo muito facilmente!
Sim, eu estou falando dos discos de corte e lixadeiras!

Imagem 17 - Uma lixadeira Bosch com um disco para corte de metais
Se trata de um disco bastante fino, torna a área de cisalhamento demasiadamente pequena, ou seja, há concentração de forças num mesmo ponto. Somando isso à rotação elevada (que pode passar de 12 mil RPM em algumas máquinas), conseguimos 'decepar' um material muito mais duro que o elemento que corta-o.
Como o elemento está disposto na geometria de disco, não é possível afixa-lo num suporte metálico para aumentar sua resistência mecânica, todavia, continua havendo a possibilidade de fraturas frágeis devido a natureza do material. Para sanar este problema, tais rotores possuem dois planos de tecido de fibra de vidro entre as camadas de pó abrasivo, e tudo isso misturado com a resina aglutinante, então, a possibilidade de quebra se reduz drasticamente!
Se o atrito pode causar a simples desaceleração ou o corte de materiais, precisamos estudar a fundo um ponto crucial:
Geometria
O uso de determinados materiais para a confecção de um equipamento dependem também da geometria das peças.
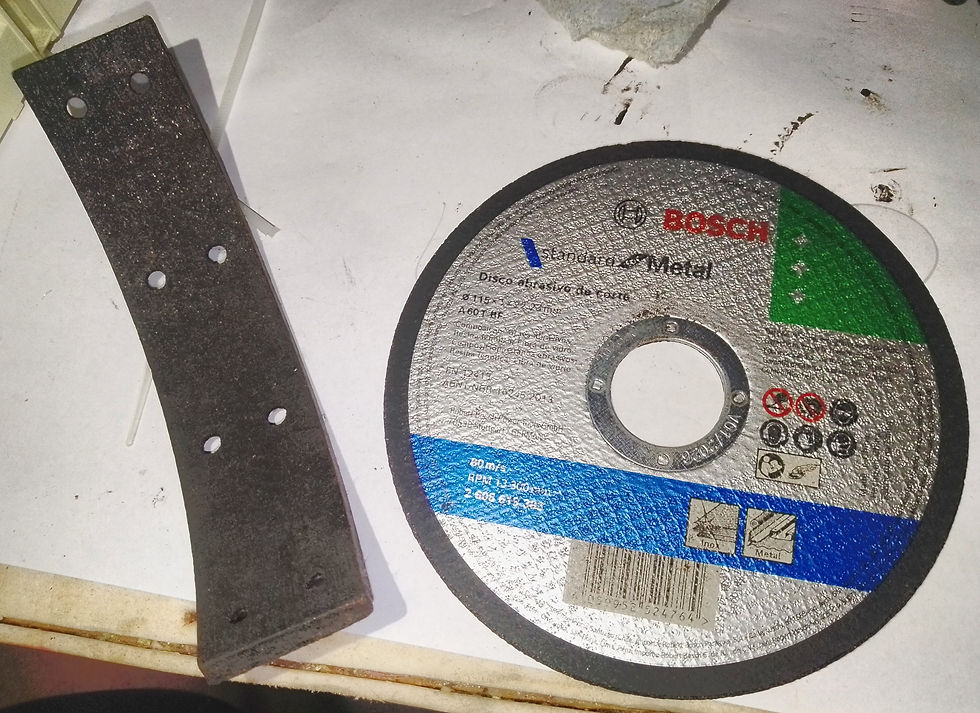
Imagem 18 - O estator abrasivo da esquerda desacelera o carro quanto fricciona no rotor metálico, já o rotor abrasivo da direita decepa estatores metálicos!
É exatamente o que foi visto no tópico "Resistência à compressão", onde foi citado o macaco garrafa com estrutura tubular em PA6-GF30.
Para tornar a "visualização mental" deste tópico melhor, vamos usar como exemplo cilindros e vasos para armazenamento de líquidos e gases...
Você já viu um semi-reboque com tanque policêntrico feito em liga de Alumínio? É algo bem raro de se achar, mas existem exemplares. Talvez, projetar um equipamento deste porte usando um material que tende a ter mais fraturas frágeis seja um grande desafio e não valha tanto assim, afinal, tanques cilíndricos usando ligas de AlMgSi são mais viáveis economicamente por aqui...
Em geral, os norte americanos costumam produzir tanques em formato elíptico (policêntricos) e auto-portantes, isto é, com um chassi integrado, irremovível, soldado à caixa de carga, independente do material de fabricação (eles adoram ligas de Alumínio!).
Vou usar como exemplo este projeto estadunidense que foi produzido em terras tupiniquins em meados de 2007:

Imagem 19 - Um semi-reboque Boreal-Heil Trailer produzido no Brasil em meados de 2007
Se na dianteira há longarinas de Alumínio soldadas ao tanque, na traseira isso fica ainda mais notável:
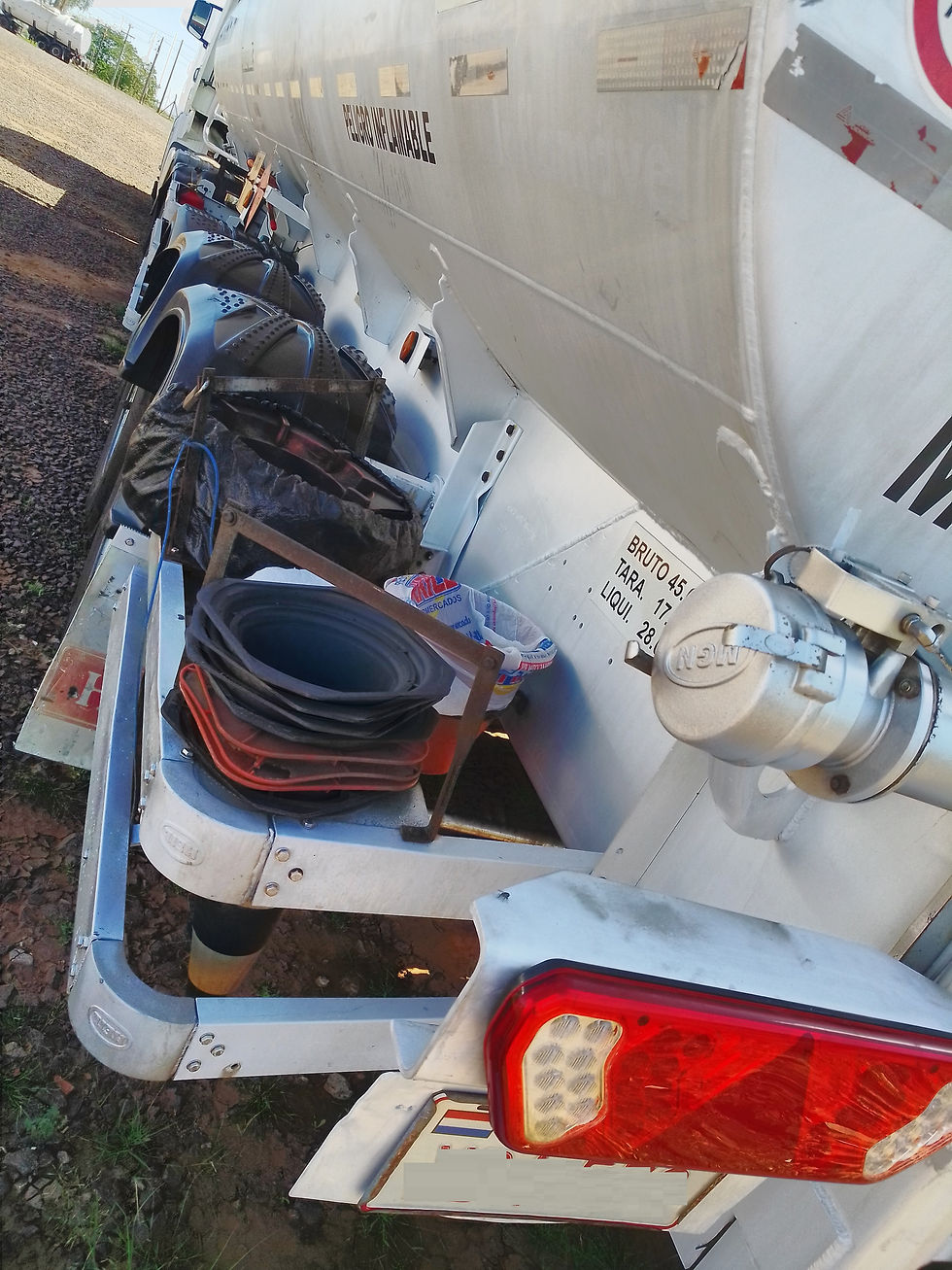
Imagem 20 - Toda a estrutura é peça única e feita de Al-5086
Os tampos possuem travessas verticais de reforço por dentro. Caso fosse compartimentado, é bem provável que as divisórias também teriam as travessas de reforço integradas, coisa que o formato cilíndrico dispensa por ter uma distribuição de esforços igualitária.
No vídeo seguinte, podemos notar que o ensaio hidrostático provoca estralos oriundos da tensionamento e destensionamento das chapas em tanques policêntricos:
Vídeo 3 - Chapas de liga de Alumínio não aguentariam tal estresse mecânico neste formato geométrico
Já no Brasil, o formato cilíndrico tem grande espaço no mercado, e o costume é criar um chassi de Aço-liga e sobre ele uma caixa de carga feita de AlMgSi, INOX 3xx ou liga de Aço. O tanque, independente do formato, possui vários berços integrados, que por sua vez são parafusados nas longarinas, como vemos na PARTE 2 deste texto, no subtópico "Resistência à vibração?".
Com estas diferenças de engenharia, consegui perceber que projetos policêntricos norte-americanos usando AlMgSi costumam render menos trincas estruturais que os projetos brasileiros, onde o tanque é parafusado ao chassi. As poucas caixas de carga elípticas criadas em territórrio nacional costumam dar problemas nas divisórias - quando não possuem reforços verticais - e nos berços - onde a vibração e as diferenças de elasticidade e flexibilidade entre os materiais resulta em parafusos frouxos e rachaduras. Por fim, dentre todas as variáveis, lembre-se que a pavimentação das estradas por aqui não costuma ser muito boa (e isso 'pesa contra' o Alumínio).
Outra coisa é o fato de apenas o formato cilíndrico aguentar alta pressão interna. Tanques elípticos sempre são feitos para transportar produtos que não formam pressões elevadas quando confinados. É por isso que reservatórios de gás nunca são policêntricos. Considere que uma "pressão elevada" neste âmbito é em torno de 100 kPA acima da pressão atmosférica. O Boreal-Heil anteriormente citado só pode 'frequentar' ensaios hidrostáticos de 30 kPA (ou 4 PSI seguindo a DOT 406), enquanto o Randon/Triel-HT e o EHBSA citados na PARTE 1 deste texto, por serem cilíndricos, podem ser testados com 273 kPA tranquilamente (ou 40 PSI seguindo a DOT 407). Já os reservatórios de gás conseguem operar na faixa dos MPA (MegaPascal) sem problemas.
Se você levar ao pé da letra, as baterias, idealmente, deveriam ter um formato sempre cilíndrico, e não prismático, como muitas são. Se, por exemplo, as baterias Chumbo-Ácido não tivessem respiros ou válvulas reguladoras de pressão, uma sobrecarga de energia culminaria num pico de geração de Hidrogênio, estufando suas paredes, podendo resultar em colapso do invólucro - que é feito de Polipropileno reforçado com carga mineral. Aliás, baterias de Lítio utilizadas em smartphones possuem formato de envelope, e é isso que acontece em sobrecargas:

Imagem 21 - Baterias prismáticas e em formato 'envelope' não são feitas pra alta pressão
Para saber mais sobre pilhas e baterias, comece CLICANDO AQUI!
Mesmo que, por exemplo, o reservatório de expansão do sistema de arrefecimento de um motor - seja ele feito de resina PP, PP+PE ou PP-GF - tenha um formato geométrico retangular ou qualquer formato complexo, existe uma 'grade' de paredes internas vasadas que interligam todas as faces da estrutura, permitindo que a pressão interna (na faixa dos 80 aos 200 kPA) não ocasione estufamento visível e ruptura do vaso.

Imagem 22 - Perceba que a geometria complexa possui várias travessas por dentro e feitas de mesmo material, que neste caso da foto é simplesmente Polipropileno
Alívio de tensões?
Quando uma peça metálica termina de ser confeccionada, ela pode passar por um "retrabalho térmico", isto é, um aquecimento com temperatura e tempo controlado seguido de um resfriamento com temperatura e tempo controlado para proporcionar um reordenamento na estrutura do ponto de vista molecular e atômico em regiões que passaram por soldas, por exemplo. É tal como fazem com os vidros no processo de têmpera, só que aí estamos falando de um alívio de tensões uniforme em toda a peça (semelhante ao processo de revenimento em ligas de Aço e Ferro Fundido).
Para saber mais sobre o processo de têmpera dos vidros, CLIQUE AQUI!
Para entender a utilidade da têmpera em ligas de aço e o posterior processo de revenimento, CLIQUE AQUI!
Ambas as leituras são importantes para entender a sequência deste texto!
No caso das ligas de aço, quando soldadas, em geral, são submetidas a um ciclo térmico caracterizado por um intenso - e relativamente rápido - aquecimento, seguido por um resfriamento também acelerado. Dependendo de outros fatores, como por exemplo sua composição química, durante este ciclo térmico podem sofrer transformação martensítica, reduzindo a ductibilidade e aumentando a fragilidade da região em questão.

Imagem 23 - Perceba que este cilíndro de gás passou por um retrabalho térmico
A transformação martensítica é adifusional, envolve um rearranjo controlado e limitado de átomos no espaço, e implica numa variação de volume, associada à mudança da estrutura cristalina CFC (Cúbica de Face Centrada) da austenita para a estrutura TCC (Tetragonal de Corpo Centrado) da martensita. Essa mudança volumétrica brusca pode acarretar a ocorrência de tensões residuais e de distorções, que em casos extremos podem causar o surgimento de trincas, conhecidas como "trincas de têmpera".

Imagem 24 - O cordão de solda feito do outro lado da chapa pode ser facilmente identificado por esse 'arco íris', que entrega o ciclo de aquecimento elevado e localizado. Se trata de um tanque feito em INOX 304, e por fora conseguimos ter noção do posicionamento dos quebra-ondas graças a essas manchas
O tratamento térmico de alívio de tensões consiste no aquecimento uniforme e controlado de um aço - seja ele soldado ou submetido a qualquer processo que gere tensões residuais - a uma temperatura especifica (inferior à temperatura crítica) por um tempo suficiente, seguido por resfriamento, também uniforme e controlado, de modo a relaxar essas tensões sem introduzir alterações microestruturais.
A temperatura e tempo de aquecimento / resfriamento dependem de fatores como a composição química da liga metálica, sua microestrutura inicial, o tamanho e a geometria da peça que está sendo tratada. O percentual de alívio de tensões internas depende destes fatores também, que coincidentemente regem o limite de escoamento.
As tensões residuais de soldagem começam a ser aliviadas a temperaturas pouco superiores à temperatura ambiente, mas é aconselhável um aquecimento lento até pelo menos 500 ºC para garantir melhores resultados, isto é, a um nível pouco inferior ao limite de escoamento do aço. Tensões residuais remanescentes após este processo dependem da taxa de resfriamento, que quando desigual pode resultar em tensões adicionais, prejudicando o efeito benéfico do tratamento.
Quanto mais próxima da temperatura crítica ou da temperatura de recristalização, mais efetiva é a temperatura de tratamento em remover as tensões residuais, desde que os ciclos de aquecimento e resfriamento sejam adequados.
O alívio de tensões afeta outras propriedades dos aços soldados, como a microestrutura, a resistência à tração e a resistência ao impacto. Assim, é necessário selecionar uma temperatura que permita atingir propriedades desejáveis e ao mesmo tempo proporcionando o máximo alívio de tensões possível.
Este processo foi inicialmente desenvolvido para juntas soldadas com grandes dimensões, que inviabilizam o tratamento no forno.
Na maioria dos metais o tratamento de alívio de tensões não modifica as características microestruturais, não substituindo outros tratamentos específicos com essa finalidade, como o revenimento.
O uso e a temperatura
Se o calor de forma controlada pode mudar as características físico-químicas de uma peça, imagina o calor de forma não controlada - ou apenas estimado para a vida útil do componente?
Já parou pra pensar que alguns sistemas provocam ciclos de aquecimento e resfriamento diariamente durante a operação da máquina?
Pois bem, um componente metálico exposto a constantes ciclos de aquecimento e esfriamento, sejam eles bruscos ou não, vai tendo sua estrutura cristalográfica modificada ao longo do tempo, tendo, por consequência, suas características elétricas e mecânicas alteradas. Eu estou me referindo à condutividade elétrica e módulos de cisalhamento e elasticidade, resultando em problemas no futuro.
Nos plásticos é mais notável o envelhecimento por calor, pois ficam frágeis, quebradiçoes, porém, com metais não fica tão aparente. Talvez das ligas mais sucetíveis ao calor sejam aquelas feitas com base em Cobre. Basta pegarmos uma chaleira elétrica, que é 'repleta' de termostatos, e veremos que é normal a perda da elasticidade em contatos de Latão ao longo de vários anos sofrendo ciclos térmicos. E aí, de uma hora pra outra, o equipamento para de funcionar por causa de um simples contato elétrico que não se fecha mais...

Imagem 25 - Há também um sinal de superaquecimento na carcaça de plástico do botão
Estas ligas de Cobre funcionam bem de maneira estatica, isto é, em sistemas imóveis, mas em aplicações dinâmicas, ou seja, em molas, por exemplo, quando expostas ao calor tendem a perder a elasticidade até chegarem em um ponto de fratura frágil.
Mais um exemplo valoroso disso está no processo de solda elétrica, onde um fluxo de corrente intenso gera uma alta quantidade de energia térmica, fundamental para a fusão dos metais a serem soldados, mas que expõe a garra e o alicate (porta-eletrodo) em situações de grande estresse térmico. Neste caso não há zinabre e o contato com as peças precisa ser o melhor possível para que a corrente flua sem barreiras (com o 'mínimo do mínimo' de resistência) e o curto-circuito tenha êxito.

Imagem 26 - Uma 'surrada' garra para solda elétrica feita em liga de aço galvanizado com contatos de Bronze
Na imagem acima vemos uma garra negativa nova para solda elétrica (da marca V8 Brasil), e junto dela capturas de um modelo também feito em liga de aço galvanizado, entretanto, com um punhado de anos de uso e bastante degradada. Notamos manchas de oxidação superfícial e uma mola de torção já sem carga.
Molas feitas com ligas de aço, independente do tipo, também perdem carga gradativamente quando expostas à ciclos térmicos frequêntes ao longo dos anos, e não apenas pelos ciclos força mecânica aplicados. O aquecimento e esfriamento proporciona uma lenta transformação martesítica que culmina num aumento gradativo das tensões na estrutura cristalina.
E é exatamente isso que ocorre também nas tubulações de escapamento dos automóveis. Só que aqui, além dos ciclos térmicos transformando a estrutura cristalina há também a ação da umidade, que se acumula dentro das caixas de ressonância e acaba gerando oxidação. É por isso que dizem que fazer uma solda pra tapar um furo ou trinca na tubulação envelhecida não é viável, pois a corrosão ocorre de dentro pra fora e o calor localizado no momento da solda vai acelerar ainda mais a transformação localizada do metal, podendo ocorrer trincas ou furos no mesmo lugar novamente, e de forma ainda mais rápida.

Imagem 27 - Uma caixa de ressonância feita em liga de INOX 4xx num Ford Focus MK1.5
A transformação da estrutura cristalina também acontece com alguns termostatos feitos com chapa de INOX 3xx. Seu espectro de dilatação em decorrência do calor acaba se modificando com o tempo...
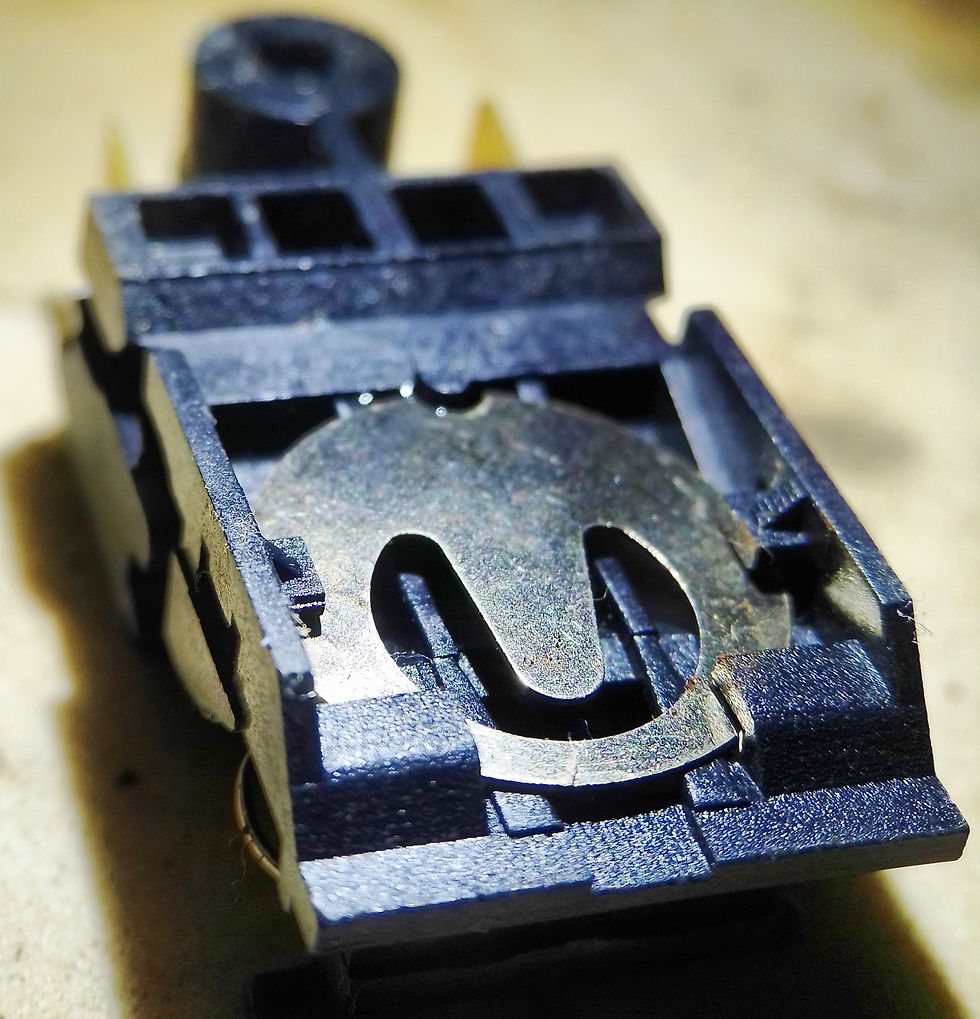
Imagem 28 - O interruptor com termostato da Imagem 24 visto de outro ângulo
CURIOSIDADE: Você pode ver mais sobre as ligas ferrosas e suas fases CLICANDO AQUI!
Isto também pode ocorrer em garras feitas de Bronze ou liga de Alumínio...
Quanto aos alicates porta-eletrodo, o desgaste também é notável, dada a composição dos condutores.

Imagem 29 - Um porta eletrodo da marca Kala
Na imagem acima vemos o uso de ferro fundido galvanizado com Cobre e a parte inferior da garra feita de liga de Cobre. O reforço da alavanca e a mola de aperto são feitos em liga de aço também galvanizado.
Em suma, o constante aquecimento e esfriamento de um condutor pode deteriorar a liga metálica que o compõe, alterando suas propriedades como se fosse um processo de têmpera proporcionado ao longo do tempo de uso.
No artigo dedicado ao Cobre, publicado aqui no HC, mostramos um borne de bateria feito de liga de Cobre com sua estrutura completamente comprometida, provando que o aquecimento pelo simples funcionamento ou pelo contato prejudicado (seja ele por uma simples folga ou acompanhado de oxidação) altera as propriedades mecânicas e elétricas da peça, comprometendo seu funcionamento e também de todo o carro.
Para saber mais sobre este exemplo do borne de bateria e sobre várias ligas de Cobre, CLIQUE AQUI!
Na figura seguinte um borne de bateria novo feito de Bronze...

Imagem 30 - Essa elasticidade é perdida com a mudança da têmpera
Este fenômeno térmico também pode ser observado em fusíveis, onde tal degradação é nomeada "envelhecimento do elo fusível". Apesar de que em fusíveis as ligas de Zinco são amplamente utilizadas, elas também se degradam pelo simples aquecimento natural decorrente do fluxo de elétrons. Você pode aprender mais CLICANDO AQUI!
Em geral, quando um veículo ou máquina, seja lá qual for, é atingido por fogo e fica danificado, não convém fazer uma restauração. Os danos provocados pela grande quantidade de calor no momento ao longo do incêndio permitem que peças metálicas tenham sua estrutura cristalográfica modificada em algum grau, além da possibilidade de deformação (isso é mais comum em ligas de Alumínio, por exemplo).

Imagem 31 - Uma quinta-roda IBERO / Fontaine parcialmente queimada num incêndio
Sabemos que a solda em Ferro Fundido é um bocado problemática, já que a alta concentração de Carbono resulta em baixa soldabilidade. Mesmo assim há métodos, procedimentos e há quem faça, e em alguns sistemas estáticos pode não haver problemas, de fato. No entanto, uma quinta-roda é uma espécie de "rolamento", um item de segurança que não pode ser remendado, sob pena de graves acidentes.
Se no próprio prato da quinta-roda acima está explícito "PROIBIDO SOLDAR", quem nos garante que esta estrutura de Ferro Fundido Nodular não teve uma transformação martensítica em algum grau devido ao incêndio? O fogo pode ter tornado-a mais frágil, isto é, menos tenaz do que antes era, permitindo que fissuras possam surgir caso remanufaturada fosse e voltasse ao uso em um caminhão qualquer...

Tornar mais claro como as forças interagem com a matéria é fundamental para se ter um panorama maior sobre a aplicabilidade de materiais, e foi essa a intenção deste artigo!
Gostou do artigo? Achou algum problema? Ficou com dúvidas? Entre em contato com Hardware Central pelo Facebook ou pelo e-mail hardwarecentrallr@gmail.com.
FONTES e CRÉDITOS
Texto: Leonardo Ritter.
Imagens, Vídeos, Gráficos e Diagramas: Leonardo Ritter; Hendrickson; Google Imagens.
Referências: Sabó; Mundo Educação; Brasil Escola; Hendrickson; Fontaine International; Jost Brasil; Sonelastic; Biopdi; Afinko Polímeros; Wikipedia (somente artigos com fontes verificadas!).
Ultima atualização: 24 de Novembro de 2024.
Comentarios